چرا نرم افزار مدیریت تولید

چرا از نرم افزار مدیریت تولید استفاده کنیم ؟
مهم ترین بخش یک سازمان و در واقع قلب تپنده آن مدیریت تولید می باشد که می توان با انتخاب یک نرم افزار مدیریت تولید مناسب کمک بزرگی به پیشرفت هرچه بیشتر سازمان کرد . از جمله کارهای این بخش برنامه ریزی ، هماهنگی ، صدور دستور کار و .... می باشد .
چرا از نرم افزار مدیریت تولید استفاده کنیم ؟
در میان نرم افزار های موجود ابتدا باید به بررسی تعدادی که به کار شما مربوط می شود را پیدا کرد و سپس برای انتخاب بهترین آن ها به مقایسه پرداخت .نرم افزار مدیریت تولید در سازمان ها به کمک نرم افزار مدیریت انبار و نرم افزرا مدیریت مالی و حسابداری بهتر کار می کند زیرا برای برنامه ریزی تولید نیاز به موجودی انبار برای ساخت محصول و همچنین تعیین بودجه موجود برای ادامه کار دارد .
چرا از نرم افزار مدیریت تولید استفاده کنیم ؟
در نرم افزار مدیریت تولید یک برنامه نویس با توجه به نیاز های شرکت مورد نظر به تحلیل ، طراحی ، مستند سازی و تست نرم افزار می پردازد . این نرم اقزار فرآیند های سنتی مدیریت را در قالب الکترونیکی و مدل سازی آن به کمک ابزار مدیریت و طراحی فلوچارت و راه کار های مدیریتی می باشد تا سازمان را به سوی اهدافش هدایت کند .
در این نرم افزار ها باید امکانات زیر موجود باشد :
- گزارش های روزانه ، هفتگی ، ماهانه ، سالانه تولید و ساخت محصول
- صدور برگ کالا های تولید شده
- ثبت اطلاعات اجناس برگشتی به خط تولید
- ثبت اطلاعات کار های در حال ساخت
- ثبت توقف تولید و دلایل آن
- بروز رسانی اطلاعات و برنامه ریزی
- پرونده ثبت موجودی
- زمان بندی برای تولید و سفارشات
- لیست مواد و قطعات موجود
- تعیین اجزاء مورد نیاز برای تولید
مزایای استفاده از نرم افزار مدیریت تولید :
برنامه ریزی بر اساس قواعد سازمان
کاهش هزینه سازمان
افزایش سرعت در تولید محصول
دقت بالا در برنامه ریزی
ارزیابی عملکرد سازمان به صورت اتوماتیک
انجام بهتر کارها
ارتباط با دیگر سیستم ها مثل نرم افزار مدیریت انبار و نرم افزار مالی و حسابداری
به روز بودن اطلاعات و ارائه آمار درست در صورت نیاز
مدیریت چیست، چه سطوحی دارد و چرا مهم است؟
مدیریت یک پدیده جهانی است. این واژه بسیار محبوب و پرکاربرد است. تمامی سازمانها، از نوع تجاری، سیاسی، فرهنگی و اجتماعی همگی با مفهوم مدیریت سروکار دارند. مدیریت است که هر تلاشی را در مسیر رسیدن به یک هدف از پیش تعیین شده، هدایت میکند.
هارولد کونتز که یک تئوریست آمریکایی کسب و کار است، اعتقاد دارد که مدیریت، هنر انجام کار با همراهی افرادی است که در گروههایی رسمی و سازمانیافته کنار هم جمع شدهاند. مدیریت هنر ایجاد محیطی است که افراد در آن قابلیت فعالیت موثر داشته باشند و در راستای نیل به اهداف جمعی، همکاری کنند.
فردریک وینسلو تیلور، پدر مدیریت علمی، این عبارت را چنین تعریف میکند:
مدیریت هنر پاسخ دادن به پرسشهای زیر است: چه کاری باید انجام شود، در چه زمانی باید انجام شود و چه باید کرد تا در بهترین و ارزانترین شکل ممکن انجام شود؟
مدیریت یک فعالیت هدفمند است. این اصطلاح را میتوان فرآیند همکاری با سایر افراد برای دستیابی کارآمد به اهداف سازمانی نیز دانست. البته باید توجه داشت شخصی که وظیفه مدیریت را به عهده میگیرد، منابع محدودی در دست دارد. او باید بتواند در دنیای در حال تغییر امروزی، از منابع خود حداکثر استفاده را ببرد تا در پر بازدهترین شکل ممکن، اهداف سازمان را محقق کند.
این وظیفه مدیریت است که با ایجاد شرایط مناسب، زمینه عملکرد پربازده و موثر را برای افراد فراهم کند. کسب اطمینان از در دسترس بودن مواد اولیه، تعیین دستمزد و حقوق ماهیانه و تدوین قوانین و مقررات جزو همین وظایف هستند.
بنابراین، میتوان گفت که مدیریت خوب، از دو عنصر کارآمدی و بازدهی بالا تشکیل شده است؛ کارآمدی یعنی کار درست را انجام دهیم و بازدهی، یعنی کار را به درستی، با کمترین هزینه و پایینترین اتلاف منابع به پایان برسانیم.
مهمترین مهارتی که زمینه را برای دستیابی به دو عنصر ذکر شده افزایش میدهد، مهارت تصمیمگیری است؛ به جرات میتوان ادعا کرد که مهمترین وظیفه هر مدیر تصمیمگیری است و منشا اصلی آنچه مدیر خوب را از مدیر بد متمایز میکند، در تصمیماتی است که گرفته میشود.
سطوح مدیریتی کدامند؟
عبارت «سطوح مدیریتی» به مرزبندیهایی اشاره دارد که بین جایگاههای مدیریتی یک سازمان وجود دارد. هر چه اندازه کسبوکار و تعداد نیروهای انسانی بیشتر باشد، تعداد سطوح مدیریت هم افزایش پیدا میکند. سطح مدیریتی نشانگر میزان قدرت، اختیارات و مقامی است که به هر جایگاه مدیریتی داده میشود. این سطوح مدیریتی را میتوان به سه دسته کلی تقسیمبندی کرد:
۱) سطح عالی
۲) سطح میانی
۳) سطح عملیاتی یا خط مقدم
مدیرانی که در هر کدام از سطوح مذکور به فعالیت مشغولاند، وظایف مختص به خود را دارند که در اینفوگرافیک زیر به شکلی مختصر و مفید به آنها پرداخته شده است.
سطوح مختلف مدیریتی و مسئولیتهای هر کدام از آنها
سطوح مختلف مدیریتی و مسئولیتهای هر کدام از آنها
چرا مدیریت مهم است؟
مدیریت را میتوان کلیدیترین نقش در هر سازمان یا شرکت دانست. کسانی که به شغلهای دیگری مشغولاند، پس از اتمام ساعات کاری و تحویل نتیجه کار، وظیفه دیگری ندارند؛ ولی مدیر کسی است که هیچگاه کارش به پایان نمیرسد و در همه حال باید به دنبال برداشتن گامهای مناسب در راستای رسیدن به اهداف شرکت باشد. دلایل اهمیت مدیریت به شرح زیراند:
مدیریت
کمک به دستیابی به اهداف تیمی:
مدیر فاکتورهای تولید را نظم و ترتیب میدهد، منابع را گردآوری و سازماندهی میکند و این منابع را به شکلی موثر با یکدیگر ترکیب میکند تا مسیر را برای رسیدن به هدف هموار کنند. در واقع کسی که نقش مدیریت را به عهده دارد، فعالیتهای گروهی را در راستای رسیدن به اهداف معین، هدایت میکند. هدفی که در تمامی سازمانها مشترک است، عبارت است از: جلوگیری از اتلاف زمان، پول و نیرو.
بهینهسازی استفاده از منابع:
مدیر موظف است که از تمامی نیروهای فیزیکی و انسانی در بهترین شکل ممکن خروجی بگیرد. این امر به افزایش بازدهی کمک میکند. شخصی که وظیفه مدیریت را به عهده دارد، باید از متخصصان، کارشناسان و سایر نیروهای کار به گونهای استفاده کند که مهارتها، دانش و تلاشهای آنها بیشترین سودآوری را داشته باشد و اتلاف به حداقل برسد. اگر تمامی کارکنان و ماشینها در بالاترین سطح عملکردی خود فعالیت کنند، هیچ نیرویی به هدر نخواهد رفت.
کاهش هزینهها:
یک مدیر موفق، درست برنامهریزی میکند و با بهکارگیری کمترین میزان ورودی، بیشترین مقدار خروجی را تولید میکند. فردی که به سمت مدیریت منصوب شده است، منابع مالی، انسانی و فیزیکی را در بهینهترین شکل ممکن در کنار هم قرار میدهد؛ نتیجه چنین اقدامی، کاهش هزینهها خواهد بود.
تشکیل یک سازمان سالم:
در فعالیتهای سازمانی هرگز نباید ردپایی از همپوشانی دیده شود. ایجاد ساختار سازمانی سالم، یکی از مسئولیتهای مدیر به شمار میرود. این ساختار باید با اهداف سازمان همراستا باشد. برای پایهگذاری چنین ساختاری، مدیر باید مسئولیتهای شغلی و دستورالعملهای ارتباطی بین افراد را تبیین کند. در واقع مدیریت است که مشخص میکند هر کس مسئولیت چه کاری را به عهده دارد، چه کسی میتواند به دیگران دستور بدهد، چه کسی مافوق است و چه کسی زیردست اوست. کسی که نقش مدیریت را به عهده دارد، مهارتها، تحصیلات و شایستگیهای هر فرد را شناسایی میکند و مطابق آنها، جایگاه شغلی مناسبی را به آنها اختصاص میدهد. در یک کلام، مدیر باید وظایف همه را به شکل شفاف تعیین کند.
برقراری تعادل:
مدیر موظف است که سازمان خود را در دنیای متغیر امروزی سرپا نگه دارد. وی همواره باید از تغییراتی که در فضای کاری سازمان او رخ میدهد، اطلاعات کسب کند. وقتی در محیط بیرونی کسب و کار تحولاتی انجام میگیرد، در داخل سازمان نیز بخش عظیمی از دستهبندیها و انتصابها باید تغییر پیدا کنند. پس یکی از کاربردهای مهم مدیریت میشود سازگاری سازمان با تقاضاهای متغیر بازار و نیازهای همواره در حال تغییر جوامع. این امر در رشد و بقای سازمان نقشی حیاتی را ایفا میکند.
کمک به شکوفایی جامعه:
مدیریت کارآمد به نتایج اقتصادی درخشان میانجامد؛ در نتیجه سطح رفاه و آسایش مردم جامعه ارتقا پیدا میکند. مدیریت خوب کارهای سخت را آسان میکند و از هدر رفتن منابع کمیاب جلوگیری میکند. در نتیجه، استاندارد سطح زندگی افزایش مییابد. هر چه سودآوری کسب و کار افزایش پیدا کند، فرصتهای شغلی بیشتری ایجاد میشود؛ درآمد مردم ارتقا پیدا میکند و در یک کلام، با کمترین هزینه بیشتر مقدار خروجی به دست میآید. دستاورد چنین مدیریتی تولید محصولات جدید و ایجاد ارزش برای جامعه خواهد بود.
اگر سمت مدیریت یک شرکت را به عهده دارید یا علاقهمندید با راهاندازی کسب و کار، به یک مدیر تبدیل شوید، سری درسهای لذت مدیریت از مجموعه یک پله بالاتر، مرجع جامعی است که شما را با تمامی مهارت و قابلیتهای لازم آشنا خواهد کرد.
برنامه ریزی تولید چیست؟
برنامه ریزی تولید قلب تپنده هر فرآیند تولیدی است و هدف آن به حداقل رساندن زمان تولید و هزینه ها و استفاده از منابع جهت افزایش بهره وری سازمان می باشد. اگر سازمان های تولیدی برای تولیدات آینده خود برنامه نداشته باشند در عرصه رقابت با مشکلات زیادی روبرو خواهند شد و دیگر قادر به ادامه حیات نمی باشند. در واقع برنامه ریزی تولید ابزاری برای زمانبندی و اولویت بندی انجام بهینه عملیات تولید محصول و پایه تصمیم گیری نسبت به قیمت توزیع و فروش محصولات است.
اهداف برنامه ریزی تولید
رضایتمندی مشتری
کمک به مدیران جهت تصمیم گیری بهتر
استفاده مناسب از منابع
کاهش هزینه های تولید ناشی از اضافه کاری
کاهش هزینه های تولید ناشی از قرارداد جنبی
کاهش هزینه های نگهداری
ایجاد یک بانک اطلاعاتی مناسب
نرم افزار برنامه ریزی تولید
در سازمان های تولیدی قبل از آنکه عملیات تولید یک محصول آغاز شود باید برنامه ریزی دقیقی بر مبنای زمان استاندارد ساخت محصول صورت گیرد تا مدیران بتوانند مقایسه ای بین بودجه دستمزد پیش بینی شده و هزینه های واقعی دستمزد انجام دهند. این کار در گذشته به دشواری صورت می گرفت اما با پیشرفت تکنولوژی و شکل گیری دانش کامپیوتر، نرم افزارهای برنامه ریزی پا به عرصه تولید نهادند تا ارائه برنامه و کنترل هزینه های دستمزد برای مدیران در امر تولید محصول امکان پذیر گردد. در حقیقت هدف اصلی اینگونه نرم افزارها مدل سازی و ارائه برنامه منظم و دقیق تولید محصول برای یک کارخانه بر اساس محدویت های تقاضا، ظرفیت تولید، انبار، بودجه و … می باشد.
نرم افزار برنامه ریزی تولیدشرکت داده پردازی بدیعان اندیشه
نرم افزار برنامه ریزی تولید شرکت داده پردازی بدیعان اندیشه برای تصمیم گیری بهتر مدیرانی طراحی گردیده است که هدف زمان بندی تولید تخصیص منابع محدود در طول زمان برای انجام گروهی از فعالیت های است. داشتن یک برنامه زمانبندی تولید مناسب، تاثیر زیادی بر افزایش کارایی و دسترسی به اهداف سازمان دارد. مدل زمان بندی تولید در هر یک از سازمانهای تولیدی با توجه به اهداف و اولویت های دسترسی به هر یک از آنها متفاوت است. بنابراین برای تعیین مدل زمانبندی مناسب در سازمان ابتدا باید اهداف، اولویت و محدودیت منابع مورد بررسی قرار گیرد.
خواهان کاهش هزینه های تولید و در نهایت افزایش بهره وری سازمان می باشند. در این سیستم برنامه ها و روشهای علمی در تولید محصول به گونه ای به کار گرفته شده است تا سازمان های تولیدی با پیشبینی مواد اولیه و تشخیص ترکیبات بهینه ی آنها در طول مدت زمان استاندارد نسبت به تولید محصولات اقدام نمایند. سیستم برنامه ریزی تولید شرکت داده پردازی بدیعان اندیشه به دلیل حجم بسیار بالای دادهها و پیچیدگی فرآیندهای تولیدی ابزاری قدرتمند در جهت موفقیت سازمان های تولیدی خواهد بود.
در چه سازمانهایی کاربرد دارد؟
نرم افزار برنامه ریزی تولید شرکت داده پردازی بدیعان اندیشه در کلیه کارخانجات و صنایع تولیدی کاربرد دارد.
چه کمکی به مدیران میکند؟
نرم افزار برنامه ریزی تولید شرکت داده پردازی بدیعان اندیشه ابزاری اقتصادی و مناسب برای برنامه ریزی سیاست های تولید محصول است. این نرم افزار به مدیران کمک می کند تا با استفاده بهینه از ظرفیت های موجود در سازمان، فرآیند تولید را بصورت دقیق زمانبندی کرده و از توقفات احتمالی تولید جلوگیری نمایند.
در چه محیطی قابل اجرا می باشد؟
نرم افزار برنامه ریزی تولید شرکت داده پردازی بدیعان اندیشه در بستر شبکه جهانی اینترنت و بدون نیاز به داشتن سخت افزار ها و تجهیزات گران قیمت می تواند ابزاری قوی برای تصمیم گیری و برنامه ریزی مدیران در جهت تولید محصولات با کیفیت بیشتر و هزینه کمتر کمک نماید.
با چه سیستم هایی در ارتباط است؟
نرم افزار برنامه ریزی تولید شرکت داده پردازی بدیعان اندیشه با سیستم های انبار (کنترل موجودی و حسابداری انبار ) و حسابداری مالی و خزانه داری در ارتباط است.
ویژگی ها و امکانات آن چیست؟
بررسی سفارشات ساخت محصول و اولویت گذاری آنها جهت صدور برنامه هوشمند تولید .
مدیریت تولید هر کالا در هر سفارش
ورود اطلاعات سفارشهای مختلف به تفکیک تاریخ برای درخواست کنندگان مختلف مانند انبارها و مشتریان مدیریت پروسه تولید بر اساس تقویم کاری و محاسبه احتیاجات خطوط تولید
مشاهده موجودی انبار و کنترل هوشمند ظرفیت تولید در هر زمان
مقایسه عملکرد تولید با دستورات ساخت محصول بر اساس برنامه ی صادر شده
بالانس کردن خطوط تولید
یافتن گلوگاههای خطوط تولید
پیش بینی اولین زمان ممکن تحویل سفارشات براساس ظرفیت منابع
ثبت اطلاعات عملکرد اجرای برنامه و تولید
ثبت اطلاعات مصارف، ضایعات و توقفات
کنترل پیشرفت سفارش مشتری
صدور رسید و حواله مصرف به سیستم انبار
محاسبات آن چگونه است؟
محاسبه امکان سنجی تولید محصول با توجه به منابع
محاسبه مدت زمان تولید محصول
محاسبه مدت زمان توقفات و خرابیهای ماشین آلات و تجهیزات تولید
محاسبه واقعی مسیر تولید و مغایرتها
گزارشات آن چیست؟
گزارشات مقایسهای مصرف مواد و میزان تولید
گزارشات دورهای انحراف از برنامه تولید
گزارشات پیش بینی اقلام مورد نیاز
گزارشات دورهای ضایعات
گزارشات توقف و دلایل آن
گزارشات زمانهای بیکاری
گزارشات کنترل انبار و تولید
گزارشات وضعیت خطوط تولید
گزارشات تخمین مدت زمان تولید محصول
گزارشات اثربخشی تجهیزات و ماشین آلات تولید محصول
موتور محرکه هر سازمان تولیدی ، برنامه ریزی و کنترل تولید است ! امروزه پویایی حاکم بر محیط تجاری ، چالش هایی همچون منابع محدود و عوامل موثر بر عملکرد را پیش روی سازمان ها قرار داده است. و مدیران را در مسیر سود آوری ملزم به برنامه ریزی با محدودیت زمانی کرده است. در واقع مدیران در زمان برنامه ریزی با عوامل نامطمئنی همچون قیمت مواد ، تضمین تقاضا ، نرخ تولید و … سر و کار دارد که باید با کنترل بر عوامل مختلف و مشخص کردن اهداف ، الویت و محدودیت منابع ، بهترین برنامه ریزی را برای استفاده از ظرفیت ها داشته باشند. در حقیقت برنامه ریزی تولید به صورت بهینه الویت و زمان بندی کارها را در بر دارد.
نرم افزار برنامه ریزی تولید آرین سیستم با قابلیت انعطاف ، به عنوان یکی از نرم افزارهای یکپارچه این شرکت علاوه بر تامین اطلاعات و ظرفیت به روز تولید ، به سازمان امکان برنامه ریزی با در نظر گرفتن اهداف ، الویت و محدودیت منابع را می دهد. با سیستم مدیریت تولید آرین سیستم ، یک مدیر تولید می تواند با اطمینان هشدارهای لازم زمان سنجی ، ظرفیت سنجی ، تحقق برنامه و … را با در نظر گرفتن توالی فرآیند تولید به موقع در اختیار داشته باشد تا با اطمینان از اطلاعات مورد نیاز بر مبنای سفارش کار ، با آرامش به فکر برنامه ریزی تولید و بهره برداری از توان تولید باشد.
کاربردهای سیستم مدیریت تولید آرین سیستم
عبارتند از:
سیستم مدیریت تولید به دلیل یکپارچگی که با دیگر سیستم ها همچون انبار ، نگهداری و تعمیرات ، کنترل مواد و بهای تمام شده دارد و همچنین بهره مندی از فرآیندهای کلیدی در تولید تا آخرین لایه BOM ، باعث می شود خطاهای انسانی به حداقل و در نتیجه بهره وری سازمان با نرم افزار برنامه ریزی تولید افزایش پیدا کند.
نرم افزارهای برنامه ریزی تولید با جمع آوری اطلاعات از قسمت های مختلف تولید به صورت منظم و سیستماتیک ، به صورت روزانه و خودکار برنامه ریزی و کنترل تولید را به صورت گزارشات دقیق به مدیر ارائه و حجم عمده ای برنامه ریزی منابع تولید و محاسبات را از دوش مدیریت می کاهد.
با به کارگیری بهترین نرم افزار برنامه ریزی تولید می توانید با دقت و همچنین تخصیص بهینه ظرفیت ماشین آلات تولید و منابع انسانی ، برنامه ریزی جامع تولید را با هدف افزایش بهره وری تولید انجام دهید و تحمیل هزینه های اضافی و مشکلات تولید را با نرم افزار مدیریت تولید به حداقل و یا حتی فرآیند پیگیری را اعمال کرد.
آیا برنامه ریزی تولید می تواند سازمان ها را در رقابت اقتصادی موفق سازد؟
در سازمانهای تولیدی، تبدیل مواد به محصولات، یک فرایند مداوم و پیوسته است و هرگونه توقفی در این فرایند هزینههای سربار تولید و بهای تمام شده محصولات را افزایش میدهد و در صورت تداوم این وضعیت، توان رقابت را از شرکت تولیدی میگیرد.
برای آن که یک سازمان تولیدی بتواند از تمام امکانات و منابع خود به درستی و در لحظه مناسب استفاده کند نیازمند برنامه ریزی دقیق منابع خود است.
منابع سازمان تولیدی بهطور اختصار 6M نامیده میشوند که عبارت است از:
- مواد اولیه Material
- ماشینآلات تولیدی Machinery
- نیروی انسانی Man power
- قالبهای تولیدی Mold
- نگهداری و تعمیرات Maintenance
- پول Money
برنامه ریزی مناسب برنامهای است که حداقل سه M از شش M فوق را پشتیبانی کند. اگر چه امروز برنامه ریزی در مورد پول کار بسیار دشواری است و معمولاً به دلیل پیچیده بودن، آن را از برنامه تولید خارج میکنند؛ با این حال تعیین برنامه زمانبندی و توالي عمليات در برنامه ريزي توليد به عنوان يكي از عوامل كليدي موفقيت محسوب میشود.
برنامه ریزی توليد سبب جلوگيري از انباشت سرمايه در موجودی داخل خط، تقليل ضايعات، كاهش و يا حذف زمان توقف ماشينآلات و تلاش براي استفاده بهتر از آنها، پاسخگویی بهموقع به سفارشهاي مشتريان و تأمین مواد اوليه و قطعات موردنیاز در موقع مناسب میشود.
هفت واحدی که در تنظیم برنامه ریزی جامع تولید نقش دارند:
برای تهیه و تنظیم یک برنامه جامع تولیدی که مهمترین منابع سازمان را در برگیرد به اطلاعات گستردهای نیاز است. ارتباط با فرایندهای اصلی سازمان مانند سفارشات فروش، تأمین کالا، گردش و موجودیهای مواد اولیه و نیمساخته، تولید دستگاههای تولیدی، ظرفیت خالی دستگاههای تولیدی و نیروی انسانی در دسترس، از ضروریات تهیه یک برنامه است. فرایندهایپشتیبان مانند برنامهریزی نگهداری و تعمیرات و کنترل کیفی نیز بر این برنامه تاثیرگذار هستند.بهطور معمول این اطلاعات در سراسر سازمان پراکنده هستند و این پراکندگی سبب میشود تا برنامه ریزی از حیز انتفاع خارج شود. هر چه بیشتر بر یکپارچگی اطلاعات تاکید شود، آنگاه فرایند برنامه ریزی تولید، کارایی بیشتری خواهد داشت. بر همین اساس برای نیل به بهرهوری، پشتیبانی و همکاری واحدهای سازمان موردنیاز است. واحدهای تاثیرگذار در این فرایند به شرح زیر هستند:
- 1)واحد برنامهریزی تولید:مسئول برنامه ریزی بوده و برای تهیه و تنظیم برنامه مناسب نیازمند داشتن ارتباط و رد و بدل اطلاعات با واحدهای مختلف سازمان است.
- 2)واحد فروش:میزان سفارش دریافتی از مشتریان و پیشبینی فروش آتی بر اساس اولویتهای مشخصشده برای ساخت و تحویل محصولات
- 3)واحد ساخت و تولید:اطلاع از تولید انجامشده توسط واحدهای مختلف تولیدی برای بهروزرسانی مقدار مواد، نیمساخته و محصولات
- 4)واحد انبارها:تحویل بهموقع مواد و کالاهای موردنیاز تولید و اطلاع رسانی برای کالاهایی که نیاز به خرید و تأمین دارند.
- 5)واحد مهندسی و ساخت:تهیه فرمولهای ساخت مراحل مختلف تولید و تنظیم نمودار گردش فرایند و نمودار فرایند عملیات تولید
- 6)واحد تدارکات:اطلاع دقیق از مواد و نیم ساخته هایموجود در انبارها و موجودیهای داخل خط تولید بهمنظور تأمین کالا متناسب با برنامه تولید.
- 7)واحد نگهداری و تعمیرات:اطلاع از برنامه ریزی نگهداری و تعمیرات دستگاههای تولید و لحاظ نمودن آن در برنامه جامع تولید.
ارتباطات فوق، ضرورت تنظیم برنامه جامع و فراگیر تولید را آشکار میسازد. عملکرد این سیستم، تأثیر زيادي بر افزایش کارایی و دسترسي به اهداف سازمان دارد. برنامهريزي توليد در واقع زمانبندی و تعيين اولويتهاي انجام كارها و اختصاص بهینه منابع در زمان مناسب است. به همین دلیل مهمترین ضرورت سازمان تلقی میگردد.
چرا یکپارچگی اطلاعات مهم است؟
ضرورت برنامهریزی بر كسي پوشيده نيست و بهطور خاص موضوع برنامهریزی در فرايند توليد گاه داراي چنان مزايايي است كه در صورت عدم وجود، سازمانهای توليدي را از مسير سالم رشد و ادامه حيات در محيط رقابتي منحرف میسازد؛ اما در این مسیر کاستیهایی نیز وجود دارد که امکان اجرای یک برنامهریزی تولید بدون رفع این کاستیها میسر نیست. همان طور که در مطالب فوق اشاره شد؛ هماهنگی بین واحدهای مختلف، از مهمترین چالشها است. عدم همافزایی اطلاعاتی بین واحدها منجر به ناکامی برنامه ریزی تولید میشود. مجموعه اطلاعات واحدها بایستی به صورت همافزا و همزمان بر روی بستر یک نرمافزار یکپارچهبه چرخه حیات خود ادامه داده تا تولید محصولات به صورت برنامهریزیشده امکانپذیر شود.
بسیاری از سازمانها، سیستم برنامهریزی تولید دارند ولی این سیستم به معنای داشتن یک سیستم یکپارچه نیست. به دلایل فوق کاملاً مشخص است که برنامه تولید بدون ارتباط با سایر اطلاعات سازمان بی معنا است. پیادهسازی چنین سیستمهایی نیازمند یک رویکرد کلنگر است و یکپارچگی نمیتواند از طریق اجرای یک فرایند جزءنگر سازماندهی شود.
در اکثر سازمانها سیستم عملیاتی تولید و سیستم مدیریت منابع سازمان با هدف اجرای برنامهریزی تولید و مدیریت کلان سازمان به صورت یکپارچه به وجود نیامده است. اکثر ساختارهای این دو سیستم، به صورت کلنگر شکل نگرفته و ماهیتهای کاملاً متفاوت و گاهی متضاد با یکدیگر دارند. عدم یکپارچگی اطلاعاتی، کاستیها و مشکلاتی را به وجود میآورد که در زیر بهطور خلاصه به آن اشاره میشود:
زنجیره تأمین Supply Chain Management:
زمان تأمین مواد، درخواست خریدهای در راه و حتی نقدینگی سازمانباید حول محور تولید شکل گیرد و در این بین با در نظر گرفتن موجودی اقلام نیم ساخته در داخل خط تولید زمان تأمین را به بهینهترین حالت ممکن برساند. اجرای درست این زنجیره به دادههای بهنگام نیاز دارد که ارتباط آن باید در یک بستر یکپارچه با سایر سیستمها مهیا شود.
برنامهریزی کلان تولید Master Production Schedule:
برنامهریزی کلان تولید با تکیه بر ساختار برنامهریزی کلان سازمان شکل میگیرد که با تکیه بر اطلاعات فرایند کسبوکار سازمان همانند اطلاعات فروش، تحلیل بازار و پیشبینی فروش تنظیم میشود.قابلانعطاف پذیر بودن این برنامه بنا به شرایط بازار، تغییر سفارشها و ... از خصوصیاتی است که به چالاکی خط تولید مرتبط است. کاملاً واضح است که این چالاکی تنها به خط تولید مرتبط نمیشود و کلیه واحدهای مرتبط باید این چالاکی را داشته باشند.
شکافهای اطلاعاتی:
ثبت اطلاعات توسط هر واحد و جزیرهای بودن اطلاعات سبب بروز شکافهای اطلاعاتی میشود، ثبت اطلاعات تکراری و موازی در واحدها از هزینه های مهم در سازمان محسوب میشوند؛ که به نوبه خود موجب هدر رفتن زمان شده و گزارشات اشتباه و یک جانبه ناشی از این اطلاعات، تصمیمگیری را برای مدیران با مشکل مواجه میکند.
مغایرتهای کلان اطلاعاتی:
مهمترین مزیت یک سیستم اطلاعات یکپارچه تولیدی، به هم پیوسته بودن تمام عملیات سازمان است، اما در سیستمهای فاقد یکپارچگی درصورتیکه یکی از واحدها،اطلاعات را به صورت ناقص ارسال و یا دریافت نماید، همبستگی اطلاعات از بین رفته و موجب بروز مغایرتهای کلان بین واحدهای مختلف سازمان میشود. این مشکل در اکثر کارخانههایی که با سیستمهای جزیرهای و یا لینک کار میکنند به وجود میآید و مشکلات کنترلی فراوانی نیز به همراه دارد و امکان یک برنامهریزی تولید دقیق را از سازمان میگیرد.
در نرمافزارهای رایج در ایران چه نارساییها و کمبودهایی وجود دارد؟
در نرمافزارهای برنامه ریزی تولید موجود در بازار که تعداد آنها بسیار اندک است؛ بهجز ماشین آلات تولیدی، سایر منابع تولید در محاسبات گنجانده نمیشوند؛ و اگر اطلاعات سایر منابع در سازمان موجود باشد کاملاً از نرمافزار فوق منفک بوده و سایر سیستمهای جزیرهای اطلاعات را به این نرمافزار ارسال و دریافت میکنند. بهطور معمول نیمساخته ها در محاسبات تولید لحاظ نمیشوند و در نهایت یکی از ورودیهای اطلاعاتی برنامهریزی تولید که داشتن اطلاعات موجودیهای پای خط است، شفافیت خود را از دست میدهد. در شیوههای مرسوم پس از ثبت تولید میبایست حواله مصرف مواد و رسید محصول تولیدشده به صورت جداگانه در انبار ثبت گردد و در صورت عدم ثبت، مغایرتهای اساسی ایجاد میگردد. در این راهکارها تولید به عنوان یک حیاط خلوت و به عنوان کالای در جریان ساخت تلقی میگردد و از انبار مواد به تولید حواله مصرف صادر میشودو امکان رهگیری مواد داخل خط وجود ندارد.
نرمافزار برنامهریزی تولید شماران سیستم چگونه یک سازمان تولیدی را یکپارچه میسازد؟
نرمافزار برنامهریزی تولید شماران سیستم با کسب تجربه از صنایع مختلف و استفاده از مفاهیم پیشرفتهای مانند MRPو MRPII راهحل عملیاتی کاملی برای کنترل و مدیریت عملیات پیچیده برنامهریزی و کنترل تولید ایجاد کرده است. در این نرمافزار منابع سازمان به واسطه دیدگاه جامع، با هم یکپارچه شدهاند. اگر اطلاعات در هر بخشی از سازمان ثبت شود بدلیل وجود یک بستر یکپارچه، در همان لحظه (برحسب نوع دسترسی) در اختیار همه سازمان قرار میگیرد که از ثبتهای تکراری جلوگیری به عمل میآید.
در نرمافزار برنامه ریزی تولید شماران سیستم، حداقل چهار M از شش M منابع قابل برنامه ریزی، لحاظ شده که عبارت از برنامه ریزی ماشین آلات، مواد؛ قالب و برنامه ریزی نگهداری و تعمیرات. این منابع به صورت کاملاً یکپارچه با هم تعامل دارند. علاوه بر آن بخشی از برنامه ریزی نیروی انسانی نیز در این نرمافزار وجود دارد.
دوازده ویژگی منحصر به فرد نرمافزار برنامه ریزی تولید شماران سیستم
در این برنامه امکانات بسیار پیشرفتهای وجود دارد که برنامه ریزی را دقیق و جذاب میسازد. ویژگیهای برنامه ریزی تولید شماران سیستم به شرح زیر هستند:
- استفاده از اولویتهای تولید بر مبنای سفارشات دریافتی
- انجام محاسبات برنامه ریزی برمبنایOPC و FPC
- محاسبه و برنامه ریزی زمان تنظیم(Set Up)دستگاهها
- برنامه ریزی ایستگاههای کاری با توجه به ظرفیت تولید آنها
- تعریف زمانبندی و برنامه کاری هر ایستگاه تولیدی بر اساس تقویم ماهانه و سالانه
- تولید نیم ساخته و محصولات و چیدمان آنها در ایستگاههای تولیدی با توجه به اولویتها
- استفاده از روشSPT در چیدمان خط تولید
- استفاده از بچهای تولیدی هر محصول برای زمانبندی هر ایستگاه
- محاسبه برنامه کار هر ایستگاه با دقت و حساسیت بر مبنای ساعت و دقیقه شروع و خاتمه تولید
- محاسبه توقفات برنامهریزیشده مانند تعمیرات، ناهار و نماز و یا عدم دسترسی موقت دستگاهها
- محاسبه احتیاجات مواد بر اساس زمان تأمین(Lead Time) و تأمین توسط پیمانکاران
- نمایش گرافیکی زمان تولید و توقفات هر ایستگاه و میزان تولید هر قطعه
در نرمافزار برنامهریزی تولید شماران سیستم به سبب یکپارچگی ایجادشده، با ثبت هر گزارش تولید ثبتهای مرتبط لحاظ گردیده و به همین سبب موجودیهای داخل خط و نیم ساخته ها بهطور دقیق محاسبه و در برنامهریزی تولید محاسبه میشوند.
این نرمافزار برای کنترل زمانبندی تولید کالا برای هر خط و نیز کنترل مواد اولیه لازم برای ساخت بر مبنای فرمول ساخت و FPCو نیز برنامهریزی سفارشهای تولید بر اساس اولویتبندیهای ایجادشده است.
این نرمافزار از مرحله سفارش کالا و یا برنامه تولید شروعشده و کنترلهای هوشمندی روی موجودی مواد، رزرو مواد اولیه، موجودی انبار پیمانکاران و کنترل مواد جایگزین با امکان مشخص کردن انبارهای تأثیرگذار در برنامهریزی پیادهسازی میگردد.
در این سیستم برنامهریزی سالانه و ماهانه و سفارش کار صورت گرفته و برای انواع عملیات تولید انبوه و یا پروژهای قابلاجرا است. بهمنظور کنترل دقیقتر و برنامهریزی منظم برای تولید محصولات و همچنین افزایش بهرهوری و راندمان خطوط تولید که منجر به کاهش هزینه و بهای تمامشده میگردد، نرمافزار برنامهریزی تولید شماران سیستم منطبق با نیازهای گروههای مختلف تولیدی و صنعتی طراحیشده است.
از دیگر امکانات این نرمافزار امکان تعریف (FPC (Flow Process Chart نمودار فرایند جریان و نمودار فرایند عملیات ( OPC (Operation Process Chart است که عملیات مختلف مانند تولید، کنترل، حملونقل، ذخیرهسازی، در انتظار، جایگزین و ... را در عملیات برنامهریزی تولید امکانپذیر میسازد.
استقرار نرمافزار برنامهریزی تولید شماران سیستم چه پیامدهایی دارد؟
استفاده از نرمافزار برنامه ریزی تولید شرکت شماران سیستم مزایای زیر را برای سازمانهای تولیدی در بردارد:
- كمك به مسئولين خط توليد در برنامهریزی بهينه توليد
- افزايش قدرت پیشبینی وضعيت توليد و در نتیجه كمك به تصمیمگیری در پذيرش سفارشها
- كاهش یا افزایش برونسپاری با استفاده از نتایج راندمان داخلی شرکت
- استفاده بهينه از توان ماشینآلات و پرسنل
- مديريت بهتر محصولات، قطعات و ضايعات
- تعيين برنامه بهينه توليد هر ماشين و ایستگاه کاری
- كاهش زمان بيكاري ماشینآلات و انتظار براي دريافت قطعه نيمساخته
- كمك به تصمیمگیری در زمينه بهکارگیری ماشینآلات جديد
- تحليل حساسيت عمليات توليد نسبت به تغيير شرايط مختلف
- كمك به شناسايي گلوگاهها
ویژگیهای نرمافزار برنامهریزی تولید
راهکار برنامهریزی و مدیریت تولید نوماتک بر اساس رویکردهای تولید شما سفارشیسازی میشود و میتواند به آسانی بر اساس ساختار محصول و ظرفیتهای تولید و با در نظر گرفتن منابع تولید (منابع انسانی، مواد اولیه، ظرفیت ماشینآلات و ...) برنامهریزی تولید را در افقهای بلندمدت، میانمدت و کوتاهمدت انجام دهد، دستور تولید را برای عملیات روزانه تولید تهیه کند و در صورت نیاز آن را تعدیل کند.
برنامهریزی نیازمندیهای مواد - MRP
بسته به سیاستهای تولید در هر واحد تولیدی عوامل مختلفی در تعیین نیازمندیهای مواد دخیل هستند. ممکن است در سطوح کلان، هدف کلی تولید بر اساس مدیریت تقاضای بازار، پیشبینی فروش و یا بیشینه ظرفیتهای موجود ماشینآلات در نظر گرفته شده باشد. شما میتوانید با اتخاذ هر یک از این رویکردها از یک سو در سطوح اجرایی مدیریت خرید، مدیریت انبار (مواد اولیه و محصول نهایی) و تحویل برنامهریزی کنید و از سوی دیگر برنامه تولید را بر این اساس برنامهریزی کنید.
تضمین دسترسی به موقع به مقدار مورد نیاز از مواد اولیه (یا محصول نیمهساخته یا محصولات میانی) که برای ساخت یک محصول نهایی لازم است، وظیفه اصلی برنامهریزی نیازمندیهای مواد – MRP است که محاسبات آن در برنامه تولید انجام میشود. راهکار برنامهریزی و مدیریت تولید نوماتک به شما کمک میکند بر اساس سیاستهای تولید خود، مواد اولیه مورد نیاز برای تولید را به موقع در اختیار داشته باشید و در عین حال با حفظ سطح انبار، هزینههای انبارداری را کاهش دهید.
برنامهریزی نیازمندیهای مواد
برنامهریزی ظرفیت منابع
برنامهریزی ظرفیت منابع - CRP
برای ایجاد برنامه تولید لازم است ظرفیتهای منابع تولید را به مراکز کاری تخصیص دهید. ظرفیتهای موجود بر اساس زمان آغاز و پایان عملیات، اولویت انجام عملیات، زمان توقفها، میزان استفاده از ماشینآلات و تجهیزات ارزیابی میشوند و سپس با توجه به نیازمندیهای ظرفیتی تولید، در محاسبات برنامه تولید مورد استفاده قرار میگیرند. به این ترتیب راهکار برنامهریزی و مدیریت تولید نوماتک به شما کمک میکند بر اساس افقهای برنامه تولید، ظرفیت منابع تولید را به صورت بهینه تخصیص دهید.
برنامهریزی بلندمدت
برنامهریزی تولید که محاسبات آن پیشتر به صورت دستی انجام میشد، کاستیهای فراوانی داشت؛ یکی از معضلات اصلی دقت پایین برنامه تولید در این حالت است، زیرا عوامل مختلفی بر برنامه تولید تأثیرگذار است که در نظر گرفتن همه آنها به صورت همزمان دشوار است. از سوی دیگر توقفهای برنامهریزی نشده و عوامل دیگر ممکن است اختلالاتی در فرایند تولید ایجاد کنند که در نتیجه آن برنامه تولید نیازمند تعدیل است.
اساس برنامه تولید در راهکار نوماتک به تناسب سیاستهای واحد تولیدی میتواند متفاوت باشد. ممکن است برنامه تولید بر اساس سفارشهای مستقیم مشتری یا تقاضای فروش پیشبینی شده باشد. همچنین ممکن است از سیاستهای تولیدی مختلفی در تولید، انبار و فروش استفاده شود. سیاستهایی مانند تولید برای انبارش – MTS، تولید سفارشی – MTO، مهندسی براساس سفارش – ETO و ... که هر یک الزامات فرایندی خود را دارد. در هر صورت شما به مبنایی برای برنامهریزی نیازمندیهای مواد و در نتیجه آن صدور دستور خرید مواد اولیه توسط انبار نیاز دارید. راهکار برنامهریزی و مدیریت تولید نوماتک راهکاری منعطف است که امکان سفارشی شدن به تناسب فرایند تولید شما را دارد. به این ترتیب میتوانید برنامه تولید را در افقهای بلندمدت و میانمدت تهیه کنید و نیازمندیهای تولید را در دوره تخصیصداده شده، مشخص کنید.
سپس میتوانید منابع تولید را با توجه به ظرفیتهایی که از پیش در ساختار محصول، مسیرهای تولید، شیفتها و تقویم کاری تعریف شده، به همراه توقفهای پیشبینی شده و پیشبینی نشده تولید در نظر بگیرید تا برنامهریزی و زمانبندی تولید را ایجاد کنید. به این ترتیب راهکار برنامهریزی و مدیریت تولید نوماتک به شما کمک میکند برنامه تولید بلندمدت (یک یا چند ساله) واحد تولیدی خود را محاسبه کنید و به راحتی آن را در بازههای زمانی کوچکتر، در برنامههای میانمدت و کوتاهمدت با جزئیات بیشتر مشاهده کنید.
برنامهریزی بلندمدت
دستور تولید
دستور تولید، یک برنامه اجرایی و دستوری عملیاتی است که براساس برنامه تولید در دوره زمانی کوتاهتری تهیه میشود. راهکار برنامهریزی و مدیریت تولید با در نظر گرفتن نیازمندیهای مواد و نیازمندیهای ظرفیت واحد تولیدی، محاسبات برنامهریزی تولید را انجام میدهد و دستور تولید بر اساس برنامه تولید ایجاد میشود. دستور تولید به شما میگوید یک واحد تولیدی چه مقدار ماده اولیه را در چه تاریخی برای تحقق برنامه تولید باید در اختیار داشته باشید و از ظرفیت ماشینآلات و تجهیزات به چه صورت استفاده کنید تا به بتوانید برنامه تولید را محقق کنید.
وقتی برنامه تولید را به دستور تولید تبدیل میکنید، به واسطه دید جزئیتری که در دستور تولید وجود دارد، توقفهای تولید، سفارشهای لغوشده و هر گونه تغییرات در زمانبندی سبب تعدیل در سطح تولید، بهکارگیری ماشینآلات، مواد اولیه و ... میشود. به این ترتیب با توجه به نیازمندیهای مواد، درخواست مواد اولیه (با توجه به سیاستهای تولید عموماٌ) به انبار داده میشود که در صورت عدم موجودی، منجر به صدور درخواست خرید (با مقدار و زمانبندی تحویل معین) خواهد شد (در تولیدهای گسسته سفارشگذاری بر اساس اندازه دسته محصول تولیدی (lot size) صورت میگیرد).
راهکار برنامهریزی و مدیریت تولید نوماتک به شما کمک میکند دستور تولید را به صورت عملیاتی بر اساس محاسبات برنامهریزی تولید ایجاد کنید، عملیات و اولویت عملیات برای تولید محصول نهایی را مشاهده کنید، نیازمندیهای ظرفیتی و مواد اولیه را در اختیار داشته باشید و توقفهای تولید را در نظر بگیرید.
معرفی نرم افزار مدیریت تولید اشـا
Asha MES – Manufacturing Execution System
سیستم مدیریت اجرای تولید اشا Manufacturing Execution System ، یک سیستم کنترل تولید گسترده یک کارخانه است که تمامی نمایه های تولید از جمله مهندسی محصول و ساخت، برنامه ریزی کلان تولید ظرفیت و نیازمندیهای مواد، زمانسنجی و زمانبندی تولید، کنترل کیفیت خط، مواد اولیه و محصولات، خرید و زنجیه تامین و برنامهریزی و افزایش بهرهوری منابع انسانی را در کنترل و مدیریت خود میگیرد و نرم افزار مدیریت تولید.
با توجه به توانمندی سیستم مدیریت تولید (Asha MES) سفارشیسازی و انعطافپذیری بالای آن، علاوه بر پیادهسازی الگوهای بهینه و استاندارد جهانی (Best Practice)، امکان کنترل کامل فعالتهای تولیدی کارخانه را نیز فراهم میسازد.
سیستم مدیریت تولید و سخت افزارهای کنترلی
ماشین آلات و سخت افزارهای کنترلی خط تولید نظیر PLC ها و Scadaها مهمترین منبع اطلاعات مورد نیاز نرم افزار مدیریت تولید (Asha MES) هستند که زمینه شکل گیری یک مدیریت تولید پیشگویانه و قابل برنامه ریزی را فراهم می سازند. علاوه بر آن با پیادهسازی سیستم مدیریت تولید اشا، چابکی لازم در تغییر برنامهریزی تولید با تغییر استراتژی بازار برای مجموعه فراهم میگردد.
محاسبه قیمت تمامشده، مدیریت و کنترل هزینه و افزایش بهرهوری نیروی انسانی و مدیریت ظرفیت و استفاده مفید از ظرفیتهای کارخانه از دیگر توانمندیهای سیستم مدیریت تولید اشا میباشد.
هدف نهایی پیادهسازی سیستم مدیریت اجرای تولید اشا (Asha MES) دست یافتن به یک ساختار تولیدی «ناب» میباشد تا بتوان در کمترین زمان، با بالاترین کیفیت، کمترین هزینه تولید و بهترین سرویس نیازهای مشتریان و بازار تامین گردد.
سیستم مدیریت تولید با اتصال اتوماتیک به سختافزارهای تولیدی (PLC_SCADA) اگر چه کنترل و مدیریت تولید را به عهده میگیرد اما همراه با سیستمهای مدیریت انبار اشا (Asha WMS)، زنجیره تامین (Asha SCM) و سیستم کنترل کیفیت و آزمایشگاه (Asha QCL) یک چرخه مدیریت کامل تولید را فراهم می سازند که امکان برنامهریزی کلان تولید (MPS) و برنامهریزی نیازمندیهای مواد (MRP) را نیز فراهم میسازد.
معرفی
سیستم مدیریت اجرای تولید (Manufacturing Execution System) یا به اختصار MES اجرای کامل و کنترل گسترده تولید را در یک کارخانه انجام میدهد و تمامی بخشها و مراحل تولید از جمله مهندسی محصول، روش ساخت، مدیریت اجرای تولید، کنترل کیفیت مواد اولیه، کنترل کیفیت حین تولید و تضمین کیفیت محصولات را شامل میشود.
با استقرار سیستم مدیریت تولید اشا (Asha MES) همگام با مدیریت فرایندهای اجرایی، کلیه اطلاعات تولید ثبت گردیده و در قالب گزارشهای آنلاین آنالیزی در اختیار مدیران قرار میدهد و بدینوسیله ضمن تسهیل و تسریع دسترسی به اطلاعات فرایند تصمیمگیری را بهبود میبخشد.
امکان ثبت اتوماتیک اطلاعات تولید از سختافزارهای کنترلی نظیر اسکادا، PLC و باسکول در سیستم اشا ضمن ثبت آنلاین اطلاعات، خطاهای ورود اطلاعات را نیز به حداقل میرساند.
اهداف
مهمترین هدف پیادهسازی سیستم مدیریت تولید اشا بهبود دائمی فرایند تولید میباشد. سیستمهای اجرای تولید با نهادینه کردن بهترین الگوهای استاندارد (Best Practice) اولین گام در دست یافتن به چرخه دائمی بهبود فرایند تولید را انجام میدهند به عبارت دیگر با قانونمند کردن فرایندها و کنترل و مدیریت آن، این امکان را میدهند تا فرایندهای اصلاح شده، در سازمان جایگزین الگوهای قبلی گردند. این سیستمها نه تنها جلوی اشتباهات و اعمال سلیقههای شخصی را به بهانه بهبود فرایندها میگیرند بلکه بستر مناسبی را برای بهبود فرایندها آنهم به صورت دائمی فراهم میکنند.
همچنین پیادهسازی سیستم مدیریت اجرای تولید، با حذف ورود اطلاعات اضافی در سیستمهای جزیرهای، اتصال مستقیم و لحظهای به سختافزارهای خط تولید شامل PLCها و SCADAها همچنین کنترل کیفیت مواد اولیه، نیمه ساخته و محصولات و کنترل کیفی فرایندها و پارامترهای کیفی حین تولید مهمترین پیشنیازها برای دستیافتن به تولید ناب که تولید محصول با بهترین کیفیت، کمترین هزینه در کمترین زمان میباشد را تامین مینماید.
یکی دیگر از اهداف پیادهسازی سیستم مدیریت اجرای تولید، کاهش قیمت تمامشده محصول و کنترل هزینههای تولید با به حداقل رساندن موجودی انبار، ضایعات صنعتی و دوبارهکاریها است. مدیریت زمان فرایندهای تولید و انتقال مواد و به حداقل رساندن محصولات معیوب و مرجوعی از دیگر نتایج راهاندازی سیستم مدیریت اجرایی تولید است که باعث کاهش هزینهها میگردد.
اما شاید مهمترین مزیت سیستمهای اجرای تولید توانمندی مجموعه در همراه شدن با تغییر نیازهای بازار و به تبع آن تغییر به موقع در تولید میباشد که در اصطلاح به آن چالاکی برنامهریزی تولید میگویند. سیستم مدیریت اجرای تولید از طریق مدیریت کیفیت جامعه فرایندها از جمله طراحی و مهندسی محصول، ورژنینگ و فرمولاسیون امکان پاسخگویی به نیازهای متوع بازار را فراهم میسازد.
ضرورت کم کردن دوره عمر محصول و جایگزینی سریع محصولات سریعتر با تنوع بیشتر تنها با راهاندازی یک سیستم مدیریت اجرای تولید امکانپذیر خواهد بود. مدیریت دانش از طریق سیستم و ردگیری فرایندهای مهندسی محصول منجر به حداقل رساندن فرایند طراحی و مهندسی محصولات جدید میگردد.
یکی دیگر از نتایج راهاندازی سیستم مدیریت تولید اشا حذف تمامی اتلافها در تولید و کسب و کار میباشد. این اتلافهای شامل هر آنچه میباشند که هیچ ارزش افزودهای برای سازمان نداشته و به صورت کلی عبارتند از : اتلاف حاصل از تولید مازاد، اتلاف حاصل از فعالیتهای اضافی، اتلاف حاصل از انباشت موجودی مواد اولیه، اتلاف حاصل از ضایعات تولید، اتلاف زمان تولید، اتلاف حاصل از عدم بهره وری نیروی انسانی، اتلاف ناشی از توقفات خط
کاربردها
نرم افزار مدیریت تولید اشا، انواع روشهای تولید از جمله تولید پیوسته (Continuous production system)، تولید گسسته (Discrete Manufacturing system)، تولید پروژهای (Continuous production system) و تولید سلولی (Cellular manufacturing systems) را پشتیبانی مینماید.
در سیستم تولید پیوسته معمولاً یک نوع یا انواع محدودی از مواد اولیه از یک سری ماشین آلات به طور زنجیرهای عبور نموده و پس از ایجاد تغییراتی در مواد اولیه که اغلب شامل تغییرات شیمیایی و فیزیکی میباشد به یک یا چند نوع محصول تبدیل می شوند. در این سیستم، تولید به صورت انبوه و بیشتر برای کالاهای یکسان صورت میگیرد. کارخانههای تولید فلزات، ، پالایشگاهها ، سیمان، کاشی، شیشهسازی و سرامیک، نمونههایی از سیستم تولید پیوسته هستند.
در سیستم تولید گسسته استراتژی تولید فرایندگرا بوده و این کارخانهها عموماً مجموعه متنوعی از محصولات سفارشی مورد نیاز بازار را تولید مینمایند. در این سیستمها هر چند مدت یک بار تجهیزات برای تولید فرآوردهای آماده و تنظیم شده و پس از تولید مقدار تعیین شدهای از این فرآورده، مجدداً برای تولید فرآورده دیگری آماده و تنظیم می شود. کارخانههای تولید فرآوردههای دارویی، بهداشتی از این نوع تولید محسوب میشوند.
فرایندهای پروژهای معمولا طولانی مدت و بزرگ مقیاس هستند. در این نوع کارخانهها به طور معمول فعالیتهای تولیدی جهت ساختن یک دستگاه بزرگ یا خاص بر اساس سفارش مشتری متمرکز است. در این نوع سیستمها به صورت خاص برای هر محصول به صورت یک پروژه مستقل فرایند تولید طراحی و تا مراحل نهایی اعمال میگردد. کارخانههایی که محصولات سفارشی تولید می کنند نظیر کارخانههای هواپیماسازی، کشتیسازی از این نوع میباشند.
سیستمهای سلولی از جدیدترین سیستمهای تولید در جهان صنعتی هستند. این سیستمها به منظور استفاده از مزایایی سیستمهای پیوسته و گسسته به صورت همزمان طراحی شدهند. این سیستمها مجموعهای هستند از سلولهای تولیدی پیوسته که ماشینآلات به صورت فرایند گروهی طبقهبندی شده و بدین ترتیب انعطاف تولید هم توسعه مییابد. پس از تولید انبوه قطعات مشترک در بخشهای گسسته به صورت مونتاژی امکان تولید محصول نهایی فراهم میگردد. اکثر صنایع خودروسازی امروزه بر این نوع سیستم تولید اجرا میگردند.
ویژگیهای و مزیتهای رقابتی سیستم مدیریت اجرای تولید اشا
سفارشیسازی و گزارشهای اختصاصی
اگر چه سیستم تولید بر اساس نوع آن از نظر زیرساخت و معماری سیستم از یک الگوی خاص تبعیت مینماید اما حتی صنایع یکسان نیز در پیادهسازی سیستم تولید نیاز به حجم گستردهای از سفارشیسازی دارند. سیستم اشا با ایجاد بستر مناسب به کمک تیم پروژه که از مشاوران اشا و کارشناسان تولید تشکیل میگردند این مهم را انجام میدهند. حتی در دو صنعت کاملا یکسان به طور مثال فولادسازی به دلیل طراحی کارخانه و شرایط خاص امکان دارد تا 40% سفارشی سازی نیاز باشد. به خصوص در تهیه گزارشهای کنترلی و مدیریتی این نیاز بیشتر احساس میشود
برنامهریزی تولید
راهاندازی سیستم مدیریت اجرای تولید پیشنیاز برنامهریزی تولید میباشد. برنامهریزی تولید شامل برنامهریزی کلان تولید (MPS)، برنامهریزی نیازمندیهای ظرفیت تولید (CRP) و برنامهریزی نیازمندیهای مواد اولیه میباشد که در صورت راهاندازی یکپارچه سیستم فروش و ثبت سفارشهای مشتری و سیستم خرید و انبار و مدیریت سفارشهای خرید با سیستم مدیریت تولید اشا امکان راهاندازی برنامهریزیهای تولید خواهد بود.
زمانبندی و زمانسنجی تولید
سیستم مهندسی تولید، امکان زمانسنجی مراحل تولید را فراهم ساخته و با ثبت اطلاعات تولید بستر لازم برای محاسبه بهرهوری زمانی تولید را فراهم میسازد. مهمترین مزیت زمانسنجی تولید امکان ظرفیتسنجی کارخانه میباشد که پیشنیاز راهاندازی برنامهریزی کلان تولید(MPS) نیز میباشد. شناسایی گلوگاههای تولید و برنامهریزی آنها (RCCP) نیز یکی دیگر از ویژگیهای راهاندازی سیستم مدیریت تولید اشا میباشد
ارتباط با PLCها و سایر دستگاههای کنترلی
سیستم مدیریت اجرای تولید امکان اتصال به PLCها را از طریق SCADA را فراهم میسازد. با اتصال PLCها علاوه بر اطلاعات ماشینآلات بسیاری از اطلاعات مورد نیاز تولید نیز به صورت اتوماتیک در سیستم اشا ثبت میگردد. علاوه بر PLCها سیستم اشا امکان اتصال به سایر دستگاهها از جمله اسپکترومترها و دستگاههای آزمایشگاهی را نیز در صورت بروز بودن دارا میباشد. همچنین اتصال به انواع باسکولها، بارکدخوانها و دستگاههای چاپ و حک لیزری از دیگر ویژگیهای سیستم مدیریت اجرای تولید میباشد.
پایش وضعیت تولید و بررسی تغییرات (Condition Monitoring)
سیستم مدیریت تولید اشا، در ارتباط با سیستم مدیریت نگهداری اشا امکان پایش وضعیت تولید و به تبع آن پایش وضعیت ماشینآلات را فراهم میسازد. کنترل کارکرد ماشین در بازههای زمانی و شرایط مشخص، در پیشبینی خرابی یا کارکرد نامناسب تجهیزات بسیار موثر است. پیشبینی نه تنها امکان رفع مشکلات و کارکرد بهینه تجهیزات را فراهم میکند بلکه از خرابیهای یکدفعه و بدون آمادگی که میتواند زیانهای زیادی را چه برای ماشینآلات چه در برنامهریزی تولید فراهم سازد را باعث میشود.
محاسبه قیمت تمامشده تولید
سیستم مدیریت هزینههای تولید اشا (Asha Manufacturing Cost) یکی از زیرسیستمهای مدیریت اجرای تولید است که با ثبت کلیه هزینههای تولید ضمن محاسبه قیمت تمامشده امکان شناسایی انحرافات از قیمت استاندارد را نیز فراهم میسازد. در صورت راهاندازی سیستم نگهداری و تعمیرات اشا و سیستم مدیریت مالی اشا این امکان فراهم میشود تا علاوه بر هزینههای مستقیم، هزینههای غیرمستقیم نیز محاسبه شود و امکان آنالیز و کنترل هزینهها و سربارها تامین گردد.
مدیریت توقفات تولید
توقفات تولید دلایل مختلفی دارند که میتواند ناشی از خرابی ماشینآلات یا کمبود مواد اولیه و قطعات مورد نیاز باشد. ثبت کلیه اطلاعات تولید امکان مدیرت توقفات و برنامهریزی جهت تعمیرات را به کمک سیستم اشا فراهم میکند ضمن اینکه با راهاندازی سیستم برنامهریزی تولید اشا حجم زیادی از توقفات تولید که به دلیل کمبود مواد اولیه یا عدم ظرفیت سنجی کارخانه بوجود میآید کاسته میشود.
اجرا و مدیریت استراتژی تولید
مهمترین نتیجه راهاندازی سیستم اجرای تولید، امکان اجرای برنامه استراتژی تولید است. سیستم اشا با ارائه شاخصهای عملکردی مختلف (KPI) این امکان را فراهم میسازد که به طور مثال روند افزایش تولید از طریق شاخصهای مربوطه کنترل و مدیریت شود. همچنین در مورد سایر بخشهای تولید همچون بهرهوری و کنترل هزینهها نیز گزارشهای اختصاصی اشا بازاری کارآمد در دستیابی به اهداف برنامههای استراتژی تولید میباشد.
معرفی زیر سیستم ها نرم افزار مدیریت تولید
سیستم مهندسی ساختار محصول (Engineering Product Structure Management)
این سیستم فرایند طراحی و مهندسی محصولات جدید و فرمولاسیون محصولات شیمیایی و دارویی را انجام میدهد، همچنین محاسبه قیمت استاندارد و روش ساخت و تهیه مستندات مربوطه نیز در این سیستم انجام میگیرد.
سیستم مدیریت ساختار محصول (Product Structure Management)
برای محصولاتی که در خط تولید قرار میگیرند درخت محصول و و فرمولاسیون به همراه طرحهای آزمایشگاهی و کنترل کیفیت را در این سیستم تعریف میکنند. ردگیری مواد و قطعات مصرفی در محصولات و محاسبه قیمت استاندارد نیز در این سیستم انجام میگیرد.
سیستم مدیریت تغییر و پیکربندی (Change and Configuration Management)
در فرایند رشد یا افول محصول تغییرات متفاوتی از فرمولاسیون تا روش ساخت نیاز میباشد که سیستم مدیریت تغییر و پیکربندی ضمن رهگیری تغییرات در اجرای تولید، هزینه و نیازهای لازم را نیز کنترل نموده و امکان خدمات پس از فروش را نیز طی دورههای وارانتی فراهم میسازد.
سیستم مهندسی روش تولید (Production Engineering)
براساس نوع تولید سیستم مهندسی روش ساخت، به صورت فرایندی، پروژهای یا ایستگاههای کاری برپایه استانداردهای مهندسی طراحی و به عنوان مبنای عملیاتی برای سیستم مدیریت اجرای تولید محسوب میگردد. این اطلاعات شامل کلیه ورودی و خروجیهای مراحل تولید، میزان و نوع مصرف مواد و انرژی و همچنین زمان مورد نیاز نیروی انسانی و ماشینآلات و تجهیزات را شامل میشوند
تعریف ایستگاههای کاری، ظرفیتسنجی، زمانسنجی و الگوی تخصیص منابع نیز از زیرساختهای لازم اجرای تولید میباشد که در سیستم مهندسی تولید اشا پوشش داده میشود.
سیستم اجرا و کنترل تولید (Production Execution and Monitoring)
با این سیستم مدیریت و کنترل تولید در راستای دستیابی به بهترین بهرهوری انجام میگیرد. با ثبت کلیه مواد اولیه مصرفی، افزودنیها، قطعات و قالبهای مصرفی و انوع انرژی، مصارف مستقیم تولید به کمک سیستم کنترل میشود. همچنین ثبت زمانهای تخصیص ماشینآلات و نیروی انسانی ضمن مدیریت ظرفیت ماشینآلات و عملکرد نیروی انسانی امکان محاسبه قیمت تمامشده محصولات را نیز فراهم میسازد همچنین با کنترل مصارف فوق برپایه استانداردهای مهندسی از پیشتعریف شده امکان محاسبه بهرهوری را در تمام سطوح تولید نیز عملی میشود.
سیستم کنترل کیفیت و آزمایشگاه (Quality Control and Laboratory)
این سیستم شامل طرحهای کیفی و آزمایشگاهی است که بر اساس آنها کیفیت مواد اولیه، مواد نیمهساخته حین تولید و کیفیت محصول براساس اطلاعات دستگاهها و آزمایشهای انجام شده سنجیده و روند تضمین کیفیت را فراهم میسازد. این سیستم به خصوص در صنایع دارویی و شیمیایی بسیار مهم بوده و با تعریف آزمایشهای گوناگون دورهای پیشنیاز سیستم اجرا و کنترل تولید میباشد.
سیستم مدیریت انرژی (Engineering Product Structure Management)
این سیستم کنترل و مونیتورینگ مصرف انواع انرژی شامل برق، گاز، نفت و آب را انجام داده و در نهایت با مقایسه استانداردهای مصرف امکان محاسبه بازدهی و هزینههای مستقیم مصرف انرژی را فراهم میسازد
سیستم بهداشت، ایمنی و محیط زیست (health Safety and Environment)
بهداشت، ایمنی و در کنار آن محیط زیست امروزه از مهمترین پارمترهای ارزشگذاری به خصوص در صنایع بزرگ میباشند. معاینههای دورهای، پرونده سلامت و مهتر از آن تامین ایمنی حین کار نه تنها یک الزام انسانی است بلکه به صورت مستقیم در عملکرد تولید و انگیزه نیروی انسانی تاثیر دارد. به کمک سیستم Asha HSE و البته برنامهریزیهای آموزشی مورد نیاز میتوان به صورت اصولی جلوی بسیاری از اتفاقات ناگوار را گرفت.
سیستم قیمت تمامشده (Cost Manufacturing System)
در نرم افزار مدیریت تولید با اجرایی شدن سیستم مدیریت اجرای تولید امکان راهاندازی سیستم قیمتتمامشده تولید نیز فراهم میشود. این سیستم با محاسبه هزینههای مستقیم تولید شامل مصرف مواد اولیه، افزودنیها، قطعات مصرفی و انرژی و همچنین هزینههای مستقیم نیروی انسانی و محاسبه کلیه سربارها امکان محاسبه دقیق قیمت تمامشده، آنهم به تفکیک دستور کارها یا مراحل تولید را فراهم میسازد. با مقایسه قیمت تمام شده واقعی با هزینههای استاندارد امکان ردگیری مغایرت قیمتتمامشده، شامل مغایرت قیمت و مصرف مواد اولیه، افزودنیها، قطعات مصرفی و انرژی و همچنین مغایرت هزینههای نیروی انسانی و سربارهای تولید را نیز فراهم میسازد.
نرم افزار جامع برنامه ریزی،زمان بندی و کنترل عملیات تولید
هسته فناور
نام شرکت: آوید سامانه رایمون
نرم افزار جامع برنامه ریزی زمان بندی و کنترل تولید
نماینده شرکت: میلاد سخنگو
ایمیل: Milad.sokhangoo@yahoo.com
پس از بررسیهای انجام شده در بیش از 60 سازمان تولیدی در صنایع دارو، غذا، و خودرو دریافتیم ، نرم افزاری جامع که توانایی پوشش کامل فرایندهای برنامه ریزی و کنترل تولید را داشته باشد در ایران موجود نیست و سازمان ها برای رفع نیاز خود مجبور به استفاده از نرم افزار های اکسس ، اکسل و یا نرم افزار های غیر جامع و متفرقه میباشند که علاوه بر عدم پوشش کامل نیاز های مدیریت تولید، قابلیت اتصال به سیستم های پایه ی مالی و بازرگانی موجود در سطح سازمان ها را نیز ندارد که این موضع گسستگی دیتابیس ها را به همراه داشته و در نتیجه آن امکان دریافت گزارشات کاربردی جامع و آنلاین را از سازمانها سلب مینماید.
بر همین اساس برآن شدیم که نرم افزار "جامع برنامه ریزی زمانبندی و کنترل تولید" را با ویژگی Database مشترک و با تکنولوژی موتور تولید فرم و جریان کاری، طراحی و تولید نماییم که به واسطه ی آن بتوانیم یکپارچگی را در دیتابیس سازمان حفظ نمائیم و انعطاف لازم جهت اعمال تغییرات دلخواه توسط کاربران را نیز فراهم آوریم.
”نرم افزار جامع برنامه ریزی زمانبندی و کنترل تولید“ متشکل از سیستمهای زیر می باشد:
1-اطلاعات مهندسی ساخت 2- برنامه ریزی عملیات تولید 3- سفارش گزاری تولید 4- برنامه ریزی زمانبندی تولید 5- ثبت عملکرد تولید 6- برنامه ریزی احتیاجات مواد
نقطه قوت این مجموعه، ”نرم افزار برنامه ریزی زمانبندی تولید“ است که توانایی پوشش انواع تولید پیوسته، گسسته یا کارگاهی را دارا میباشد. سیستم مذکور با ویژگیهای نام برده شده برای اولین بار در ایران به واسته تکنولوژی موتور تولید فرم و جریان کاری در دست طراحی و تولید قرار گرفته است. که قابلیت اتصال به دیتابیس های پایه ای سازمان را نیز دارا میباشد.
نرم افزار ساخته شده جامع برنامه ریزی،زمان بندی و کنترل عملیات تولید برای اولین بار در ایران در برنامه ریزی زمان بندی و کنترل عملیات تولید ، مدیریت GIT،مدیریت حمل و نقل تولید کاربرد دارد.
تصاویر بخشی از نرم افزار ساخته شده:
با توجه به مشکلات موجود در صنعت برآن شدیم نرم افزار "جامع برنامه ریزی زمانبندی و کنترل تولید" را با ویژگی Database مشترک طراحی و تولید نماییم که به واسطه آن بتوانیم یکپارچگی را در دیتابیس سازمان حفظ نماییم و انعطاف لازم جهت اعمال تغییرات دلخواه توسط کاربران را نیز فراهم آوریم.
نرم افزار جامع " برنامه ریزی زمانبندی و کنترل تولید" متشکل از سیستمهای زیر می باشد:
اطلاعات مهندسی ساخت
برنامه ریزی عملیات و سفارشگذاری تولید
برنامه ریزی و زمانبندی تولید
سیستم بالانس خط
سیستم شارژ خط تولید
برنامه ریزی احتیاجات مواد
ثبت عملکرد تولید
ردیابی تولید
زیر سیستم کنترل عملیات تولید
زیرسیستم تولید بهنگام (JIT)
کنترل کیفیت تولید
این مجموعه توانایی پوشش انواع تولید پیوسته، گسسته یا کارگاهی را دارد و قابلیت اتصال به دیتابیس پایه سازمانها را نیز دارا میباشد.
اطلاعات مهندسی ساخت:
سیستم اطلاعات مهندسی ساخت با دریافت اطلاعاتی همچون ساختار محصول، ضریب مصرف قطعات، عملیاتهای تولید، بچهای انتقالی، دستگاه و اپراتور و ایستگاهای کاری میتواند امکان تخصیص BOMهای متفاوت به یک محصول، تعیین جریان کاری در هر BOM، تفکیک عملیات به انواع تولید، مونتاژ، حمل و نقل، جابجایی، پیمانکاری، و عملیات مرتبط با کنترل کیفی را برای مشتری فراهم نماید.
از دیگر ویژگیهای این نرمافزار می توان به موارد زیر اشاره نمود:
تعریف عملیات برای فرآیند تولید یک محصول و تخصیص دستگاههای تولیدی، اپراتور، وسایل نقلیه و ایستگاه به هر عملیات
ثبت شاخص جهت تعیین میزان ضایعات، زمان راهاندازی، زمان مورد نیاز در هر عملیات، زمان حمل و جابجایی حین تولید
امکان تکمیل هر قسمت از اطلاعات مهندسی ساخت توسط واحدهای مربوطه با بهرهگیری از تکنیک جریان کاری و نمایش کارتابلی، با حفظ ویژگی یکپارچگی داده
حفظ یکپارچگی دادهها بین سیستم تولید و سیستمهای انبار و حقوق دستمزد جاری در سازمان به منظور دریافت گزارشات مدیریتی پیچیده به وسیله فراخوانی اتومات اطلاعات کدینگ کالا و پرسنل
امکان تهیه آرشیو کاملی از نقشه ها و اطلاعات قطعات
سیستم برنامه ریزی و سفارشگذاری تولید
این سیستم، جهت سفارشگذاری تولید در بازههای زمانی روزانه، هفتگی، ماهانه و سالانه کاربرد دارد و امکان انتخاب BOMهای گوناگان برای تولید یک محصول را فراهم میآورد. همچنین این سیستم پس از دریافت حجم تولید اقدام به تخمین زمان تولید، تعداد نیروی انسانی و دستگاههای مورد نیاز نموده و لیست عملیاتها را به صورت درخت واره و سلسله مراتبی نمایش میدهد.
ویژگی ها:
امکان دریافت سفارشات تولید و اولویت بندی آنها
امکان پیشبینی تجهیزات مورد نیاز جهت تولید
امکان صدور برگه تولید
امکان پیشبینی هزینه تولید
امکان تهیه پیشبینی مواد مورد نیاز
امکان تعریف سر برنامه تولید (MPS) و تعیین میزان تولید از هر محصول در بازههای زمانی تعیین شده
امکان ارزیابی ظرفیت تولید و تصمیمگیری برای تغییر MPS
سیستم برنامه ریزی و زمانبندی تولید
این سیستم اطلاعات تاریخ تحویل، حجم محموله، انواع عملیاتها مورد نیاز تولید و... را دریافت مینماید و جهت اعمال زمانبندی تولید و تعیین زمان شروع و پایان هر عملیات به کار میرود و قابلیت پوشش کامل نیازهای انواع خطوط تولید شامل گسسته، پیوسته، ترکیبی و پروژهای را دارد. همچنین این سیستم میتواند زمان setup دستگاهها، انواع زمان توقفات و انواع موازیکاری (دستگاهها، پرسنل و خطوط تولید) را در محاسبات زمانبندی خود اعمال کند. با توجه به نوع اطلاعات مندرج در این سیستم امکان تعیین انحراف زمان تولید و مشخص نمودن دلایل آنها نیز وجود دارد. امکانات دیگری که این سیستم برای مدیران فراهم میآورد برآورد بسیار دقیق انواع ظرفیت تولید و همچنین بررسی دقیق و در لحظه گلوگاهها میباشد. از دیگر کاربردهای این نرمافزار میتوان به مدیریت دقیق و در لحظه مراحل تولید، تعیین هزینه دقیق نیروی انسانی و دستگاههای مورد استفاده، مدیریت دقیق زمانبندی تولید، مدیریت دقیق گلوگاهها، بالانس ظرفیت ایستگاه و خطوط تولید،کاهش زمان تولید، بررسی مشکلات زمانبندی و زمانسنجی ایستگاههای تولیدی، امکان تعیین کمبود ظرفیت نیروی انسانی و دستگاهها، تعیین شاخص زمان بهینه تولید و مقایسه عملکرد زمانی تولید به تفکیک روز، هفته، ماه و سالیانه جهت افزایش راندمان تولید، اشاره نمود.
ویژگیهای سیستم:
نمایش کارتابلی سفارشگذاری و زمانبندی تولید
مشخص نمودن مدت زمان انحراف از برنامه
امکان نمایش کارتابلی بیشترین علل ایجاد تاخیر در برنامه
امکان نمایش مراحل دارای بیشترین تاخیر به تفکیک خط، ایستگاه، دستگاه و اپراتور
امکان نمایش تعداد برنامههای بررسی نشده توسط مدیریت
امکان تعیین شاخصهای زمانبندی تولید و محاسبه میزان انحراف از استاندارد زمان تولید
امکان اعمال زمان موازی کاری و زمان راه اندازی در محاسبات
سیستم بالانس خط تولید:
این سیستم جهت تعیین بهترین برنامه تولید بر اساس ظرفیت موجود سازمان مورد استفاده قرار میگیرد. این سیستم با توجه به مقدار سفارشگذاری محصولات، تاریخ تحویل، اولویت تولید و ظرفیت موجود در شیفتهای زمانی متفاوت، بهینهترین برنامه تولید را براساس زمان یا هزینه ارائه می نماید. تعیین دقیق ظرفیت موجود در شیفتهای متفاوت، ظرفیت مورد نیاز جهت تأمین سفارش و همچنین توانایی برنامهریزی با عملیات های یکسان و موازی از دیگر ویژگیهای مهم این سیستم میباشد.
ویژگی ها:
بالانس خط جهت تولید چندین محصول
استفاده بهینه از ظرفیت موجود
برنامهریزی با BOM های متفاوت
مشخص نمودن گلوگاهها
برنامهریزی بر اساس گلوگاهها
پیشنهاد بهترین استراتژی جهت تولید
سیستم شارژ خط تولید:
این سیستم جهت برنامه ریزی و زمانبندی حمل و نقل از زمان بارگیری تا تخلیه مواد در خط تولید مورداستفاده قرار میگیرد. این سیستم بر اساس انواع تجهیزات حمل و نقل، ظرفیت حمل (براساس وزن، تعداد، حساسیت کالا و ...)، مسافت و زمان حمل و نقل اقدام به برنامهریزی شارژ خط تولید مینماید. همچنین این سیستم با اتصال به سیستم برنامهریزی و زمانبندی تولید، سیستم برنامه ریزی احتیاجات مواد، سیستم نت و با توجه به ظرفیت و اولویتهای حمل، برنامه کاری روزانه هر یک از وسایل حمل و نقل را مشخص مینماید.
ویژگیها:
مشخص نمودن ظرفیت دقیق حمل و نقل
استفاده بهینه از ظرفیت حمل ونقل
مشخص نمودن کمبود یا مازاد تجهیزات حمل و نقل
زمان بندی حمل و نقل
شارژ به هنگام خط تولید
مشخص نمودن میزان انحراف از برنامه حمل و نقل
مشخص نمودن عوامل مؤثر در حمل و نقل
تعیین دقیق کارکرد تجهیزات
محاسبه هزینه حمل و نقل
سیستم برنامه ریزی احتیاجات مواد
این سیستم جهت تعیین حجم مواد و ملزومات مورد نیاز در تولید مورد استفاده قرار میگیرد. همچنین با توجه به قابلیت ثبت پیشبینی زمان دریافت سفارش، امکان پیشنهاد زمان و تاریخ سفارشگذاری در آن وجود دارد. از اطلاعات این سیستم میتوان در صدور درخواست کالا از انبار و درخواست تامین استفاده نمود. از سایر کاربردهای این سیستم میتوان به تعیین حجم سفارش، وسیله نقلیه جهت دریافت مواد و سطح کیفی مواد مورد نیاز اشاره کرد. همچنین با توجه به توانایی سیستم در شناسایی موجودی سازمان در مقاطع گوناگون (موجودی سفارشات در راه، موجودی انبارها و ...) امکان تفکیک درخواست کالا وجود خواهد داشت. مدیران برنامهریزی قادر خواهند بود از یک طرف با زمانبندی مناسب برای خرید مواد و قطعات و از طرف دیگر با صدور سفارشهای به موقع برای تولید قطعات ساختنی ، ضمن ساخت و تحویل به موقع محصولات به مشتریان، هزینههای نگهداری کالا در انبار را به طور قابل ملاحظهای کاهش دهند.
ویژگیها:
دریافت اطلاعات مقدار موجودی کالا و حداقل موجودی آن از سیستم انبار
دریافت اطلاعات سفارش در راه از سیستم تدارکات و کنترل عملیات تولید
ثبت اطلاعات Lead Time خرید و ساخت کالاها
محاسبه تعیین نیازمندی خالص به هر کالا
تفکیک درخواست تامین کالا با در نظر داشتن موجودی در هر نقطه از سازمان و ارسال اتومات درخواست ها به واحد های مسئول تامین آن
سیستم ثبت عملکرد تولید
این سیستم با فراهم آوردن اطلاعات دقیق از وضعیت دوباره کاری، عملیات اصلاحی، حجم ضایعات، ظرفیت استفاده شده نیروی انسانی و دستگاه، مواد مصرفی، برنامه های تولید، میزان موجودی پای کار، عملکرد ماشینآلات و پرسنل تولید، قدرت تصمیمگیری مدیران تولید سازمانها را افزایش میدهد.
افزون بر این، به دلیل متغیر بودن فرآیند تولید که به دلایل گوناگون از جمله تغییر در اولویت تولید، تغییر در تقاضا و سفارش مشتریان، نوسان در شرایط بازار، خرابی ماشین آلات، نوسان موجودی مواد اولیه و... ایجاد می شود، سیستم باید در برنامهریزی و زمانبندی انعطافپذیر باشد تا توانایی پاسخگویی به نیاز مدیران تولید را داشته باشد.
ویژگیهای نرم افزار:
صدور برگهی کارهای تولید بر مبنای سفارشهای تولید
صدور اتوماتیک درخواست کالا از انبار بر اساس BOM محصول
امکان انجام عملیات بازرسی و کنترل کیفی در هر مرحله و اعمال کنترلهای لازم در زمان ثبت عملکرد
امکان فراهم کردن اطلاعات هزینه تولید برمبنای میزان کارکد پرسنل و دستگاه
امکان ثبت زمان کارکرد ماشین آلات جهت تنظیم برنامه نگهداری و تعمیرات
امکان ثبت حجم ضایعات، دوبارهکاریها، نامنطبق و تولیدهای سالم جهت محاسبه انحراف از استانداردهای تعیین شده در سیستم اطلاعات مهندسی ساخت
امکان محاسبه فرصت از دست رفته در تولید
امکان ثبت کارکرد ماشینآلات و پرسنل تولید و تهیه گزارش راندمان
امکان ثبت توقفهای ماشین آلات به همراه دلایل توقف
امکان مشاهده گزارش موجودی نیمه ساختههای در جریان تولید به تفکیک هر مرحله از تولید
امکان گزارشگیری از شاخصهای کلیدی عملکرد تولید
امکان محاسبه موجودی در کل سازمان و محاسبه موجودی پای کار و موجودی سیستم انبار در لحظه
سیستم ردیابی تولید
این سیستم جهت ثبت اطلاعات تولید در هر مرحله به تفکیک ایستگاه، دستگاه و یا نیروی انسانی مورد استفاده قرار میگیرد و توانایی ذخیره سازی مدت زمان و تعداد تولید در هر مرحله را نیز دارد. تفاوت این سیستم با سیستم کنترل عملیات در قابلیت ایجاد فرمولهای بارکدسازی و اتصال آن به دستگاه بارکدخوان و در نتیجه فراخوانی اطلاعات قطعات از طریق دستگاه بارکدخوان بوده که به واسطه آن امکان پیگیری وضعیت هر قطعه یا محصول پس از تکمیل و ارائه آن به بازار ایجاد خواهد شد. از این سیستم میتواند در راستای استقرار ISO-TS استفاده نمود. این سیستم جهت ایجاد آرشیو کاملی از اطلاعات زمان تولید قطعه، شخص و دستگاه تولید کننده آن به کار میرود که امکان ردیابی دقیق محصول در صورت خرابی و یافتن علت آن را فراهم می کند.
ویژگیها:
امکان تعریف فرمول بارکد متناسب با نیاز هر سازمان
امکان فراخوانی جمعی کالاهای ورودی به خط تولید
امکان ردیابی اطلاعات تولید در سطح دستگاه، اپراتور و...
امکان فراخوانی قطعات به صورت بچ در ابتدای خط تولید و فراخوانی آن در انتهای خط تولید بدون نیاز به ثبت اطلاعات در هر مرحله از تولید
زیر سیستم کنترل عملیات تولید
این سیستم قابلیت اتصال به سیستم کنترل عملیات تولید و ردیابی تولید را دارا میباشد و با در اختیار داشتن کارتابل کنترل کیفیت و توقفها در خود، امکان ثبت نتایج بازرسی و تعمیرات اصلاحی را فراهم میآورد. بنابراین در صورتی که سازمانی نیاز به اعمال اطلاعات کنترل کیفی و توقف ها داشته باشد میتواند موثر واقع شود. قابل ذکر است که امکانات این سیستم جهت رفع نیاز واحد کنترل کیفیت و تعمیرات نگهداری طراحی نشده بلکه صرفا جهت اعمال کنترل این واحدها بر جریانکاری تولید مورد استفاده قرار میگیرد.
ویژگیها:
امکان نمایش کارتابلی اطلاعات ثبت شده در هر مرحله از تولیدکه نیاز به اعمال عملیات بازرسی و کنترل کیفی دارند
امکان ثبت درخواست بررسی توقف ایجاد شده در هر مرحله از تولید و نمایش این درخواست در کارتابل پرسنل تعمیرات و نگهداری
امکان ثبت اطلاعات کنترل کیفی انجام شده برروی کالا
امکان ثبت علل توقفها، مدت زمان رفع مشکل و پرسنل مسئول
زیر سیستم تولید بهنگام(JIT)
این نرم افزار به عنوان یک زیر سیستم عمل میکند و با اتصال به سیستمهای مهندسی ساخت، ثبت عملکرد تولید یا ردیابی تولید، برنامه ریزی زمانبندی، سفارشگذاری تولید و برنامه ریزی احتیاجات مواد، امکانات زیر را در اختیار مدیران قرار میدهد تا بتوانند تمام عوامل موثر در تولید بهنگام را تحت کنترل خود درآورده و با اعمال برنامه ریزی و طرح استراتژیک مناسب، به صورت گام به گام فرهنگ تولید بهنگام را در سازمان جاری سازند.
ویژگی ها:
امکان کنترل عوامل موثر در پیاده سازی تولید بهنگام مانند: موجودی پایکار، ضایعات، زمان حمل و نقل، زمان جابجایی، زمان تولید و...
امکان شاخصگذاری برای تمام عوامل موثر در تولید
امکان بهره گیری از سیستم کانبان با اتکا به ویژگی برنامه ریزی کششی
امکان تهیه بانک اطلاعاتی جامع از تمام عوامل موثر بر تولید بهنگام
امکان تهیه گزارشات کنترلی دقیق از میزان انحراف نسبت به شاخص های تعیین شده
امکان تعیین مهمترین عوامل موثر بر انحراف از شاخصهای تولید بهنگام
امکان تعیین میزان تکرار و حجم تاثیر هر یک از عوامل ایجاد کننده انحراف در شاخص
امکان پیاده سازی فلسفه تولید بهنگام برای قسمت کوچکی از سازمان و استفاده از استراتژی توسعه گام به گام
امکان ارائه برنامه بهبود وضعیت حمل و نقل درون سازمانی
سیستم کنترل کیفیت
این سیستم جهت اعمال عملیات کنترل کیفی بر روی محصولات و نیمه ساخته های تولید شده در خط مورد استفاده قرار میگیرد. همچنین باتوجه به نوع اتصال این سیستم با سیستم ثبت عملکرد تولید و ردیابی تولید، توانایی مشاهده اطلاعات قطعات تولیدی به صورت کارتابلی و در لحظه را فراهم میکند. از دیگر امکانات این سیستم میتوان به اعمال فرمولهای آماری و انواع نمونهگیریها در کنترل وضعیت کیفی کالاها اشاره نمود. باتوجه به اطلاعات ثبت شده در این سیستم و نوع ارتباط آن باسایر سیستمهای تولیدی، این امکان برای مدیران واحدهای کنترل کیفی و تولیدی فراهم میشود تا بتوانند مهمترین عوامل کاهش کیفیت و یا افزایش آن را در لحظه تحت کنترل خویش درآورند.
ویژگی ها
امکان تهیه برنامه کنترل کیفی محصولات
امکان تهیه بانک اطلاعاتی کامل از عوامل مؤثر در کاهش کیفیت نیمه ساخته و محصولات
امکان صدور سند کیفیت بر اساس برگه کار تولید، جهت بازرسی و کنترل نیمه ساختهها و محصولات در جریان فرایند تولید
امکان ثبت عملکرد تولید بر اساس وضعیت تأیید یا رد کنترل کیفی کالا
امکان اندازهگیری و ثبت پارامترهای مهم محیط تولید و تاثیرگذار در کیفیت محصول
امکان صدور سند کیفیت بر اساس نتایج ثبتشده
امکان تهیه گزارشهای آماری
ویژگیهای نرمافزار گزارشهای تحلیلی
استفاده از راهکارهای سنتی برنامهریزی و مدیریت تولید، در فضای کسبوکار امروز کاستیهای بسیاری دارند. فارغ از اینکه راهکارهای نوین میتوانند دقت برنامهریزی تولید شما را بهبود دهند و به صورت همزمان امکان کنترل همهجانبهای را برای شما فراهم کنند، یکی از تفاوتهای عمده استفاده از راهکارهای نوین در گزارشهای تحلیلی به موقع است که میتواند مبنایی مناسب برای تصمیمگیری باشد.
آنالیز سود سرانگشتی
یکی از راهحلهای ویژه در راهکار برنامهریزی و مدیریت تولید نوماتک که به شما کمک میکند میزان سود خود را در صورت تولید سطح مشخصی از هر محصول به راحتی تخمین بزنید. آنالیز سود سرانگشتی با در نظر گرفتن پیشفرضهایی که برای تولید هر محصول (از نظر مواد اولیه، عملیات، ماشینآلات، مراکز کاری، توقفها و ...) تعریف کردید، محاسبات خود را انجام میدهد. این امکان به ویژه برای محاسبات سرانگشتی و تعیین سطح تولید برای تحقق اهداف فروش بسیار کاربردی است.
درخواست دمو
آنالیز سود سرانگشتی
گزارشهای مقایسهای سطح تولید
گزارشهای مقایسهای سطح تولید
شما میتوانید در هر لحظه، در بازههای مشخص و به تفکیک مراکز کاری، محصول و ... مقدار تولید خود را مشاهده کنید، گزارش تولید گونهها و درجههای مختلف کالا (درجه 1، درجه 2، درجه 3و ...) را بر اساس تعریفهایی که پیشتر در سیستم انجام دادید، بررسی کنید و در صورت نیاز این مقادیر را با مقادیر دورههای زمانی مشابه مقایسه کنید. همچنین میتوانید سطح تولید محقق شده را با برنامه تولید مقایسه و دلایل کاهش تولید را بررسی کنید.
درخواست دمو
گزارشهای توقفهای تولید
گزارشهای توقف، زمانهای توقف و دلایل آن به صورت کامل در دسترس شماست. همچنین میتوانید انحرافات از برنامه تولید یا مصرف را با مقایسه سطح واقعی تولید با برنامه تولید کنترل کنید.
درخواست دمو
گزارشهای توقفهای تولید
گزارشهای استفاده از منابع تولید
گزارشهای استفاده از منابع تولید
سطح استفاده از ظرفیت دستگاهها و ماشینآلات، بازده نیروی انسانی و همچنین گزارشهای بازدهی نیروی انسانی، اثربخشی جامع تجهیزات OEE، عملکرد ماشینآلات و نیروی انسانی از مسائلی است که میتوانید در هر لحظه از آن بهرهمند شوید.
و گزارشهای دیگری که به تناسب نیازمندیهای کسبوکار خود میتوانید در اختیار داشته باشید.
ویژگیهای نرمافزار برنامهریزی تولید
راهکار برنامهریزی و مدیریت تولید نوماتک بر اساس رویکردهای تولید شما سفارشیسازی میشود و میتواند به آسانی بر اساس ساختار محصول و ظرفیتهای تولید و با در نظر گرفتن منابع تولید (منابع انسانی، مواد اولیه، ظرفیت ماشینآلات و ...) برنامهریزی تولید را در افقهای بلندمدت، میانمدت و کوتاهمدت انجام دهد، دستور تولید را برای عملیات روزانه تولید تهیه کند و در صورت نیاز آن را تعدیل کند.
برنامهریزی نیازمندیهای مواد - MRP
بسته به سیاستهای تولید در هر واحد تولیدی عوامل مختلفی در تعیین نیازمندیهای مواد دخیل هستند. ممکن است در سطوح کلان، هدف کلی تولید بر اساس مدیریت تقاضای بازار، پیشبینی فروش و یا بیشینه ظرفیتهای موجود ماشینآلات در نظر گرفته شده باشد. شما میتوانید با اتخاذ هر یک از این رویکردها از یک سو در سطوح اجرایی مدیریت خرید، مدیریت انبار (مواد اولیه و محصول نهایی) و تحویل برنامهریزی کنید و از سوی دیگر برنامه تولید را بر این اساس برنامهریزی کنید.
تضمین دسترسی به موقع به مقدار مورد نیاز از مواد اولیه (یا محصول نیمهساخته یا محصولات میانی) که برای ساخت یک محصول نهایی لازم است، وظیفه اصلی برنامهریزی نیازمندیهای مواد – MRP است که محاسبات آن در برنامه تولید انجام میشود. راهکار برنامهریزی و مدیریت تولید نوماتک به شما کمک میکند بر اساس سیاستهای تولید خود، مواد اولیه مورد نیاز برای تولید را به موقع در اختیار داشته باشید و در عین حال با حفظ سطح انبار، هزینههای انبارداری را کاهش دهید.
درخواست دمو
برنامهریزی نیازمندیهای مواد
برنامهریزی ظرفیت منابع
برنامهریزی ظرفیت منابع - CRP
برای ایجاد برنامه تولید لازم است ظرفیتهای منابع تولید را به مراکز کاری تخصیص دهید. ظرفیتهای موجود بر اساس زمان آغاز و پایان عملیات، اولویت انجام عملیات، زمان توقفها، میزان استفاده از ماشینآلات و تجهیزات ارزیابی میشوند و سپس با توجه به نیازمندیهای ظرفیتی تولید، در محاسبات برنامه تولید مورد استفاده قرار میگیرند. به این ترتیب راهکار برنامهریزی و مدیریت تولید نوماتک به شما کمک میکند بر اساس افقهای برنامه تولید، ظرفیت منابع تولید را به صورت بهینه تخصیص دهید.
درخواست دمو
برنامهریزی بلندمدت
برنامهریزی تولید که محاسبات آن پیشتر به صورت دستی انجام میشد، کاستیهای فراوانی داشت؛ یکی از معضلات اصلی دقت پایین برنامه تولید در این حالت است، زیرا عوامل مختلفی بر برنامه تولید تأثیرگذار است که در نظر گرفتن همه آنها به صورت همزمان دشوار است. از سوی دیگر توقفهای برنامهریزی نشده و عوامل دیگر ممکن است اختلالاتی در فرایند تولید ایجاد کنند که در نتیجه آن برنامه تولید نیازمند تعدیل است.
اساس برنامه تولید در راهکار نوماتک به تناسب سیاستهای واحد تولیدی میتواند متفاوت باشد. ممکن است برنامه تولید بر اساس سفارشهای مستقیم مشتری یا تقاضای فروش پیشبینی شده باشد. همچنین ممکن است از سیاستهای تولیدی مختلفی در تولید، انبار و فروش استفاده شود. سیاستهایی مانند تولید برای انبارش – MTS، تولید سفارشی – MTO، مهندسی براساس سفارش – ETO و ... که هر یک الزامات فرایندی خود را دارد. در هر صورت شما به مبنایی برای برنامهریزی نیازمندیهای مواد و در نتیجه آن صدور دستور خرید مواد اولیه توسط انبار نیاز دارید. راهکار برنامهریزی و مدیریت تولید نوماتک راهکاری منعطف است که امکان سفارشی شدن به تناسب فرایند تولید شما را دارد. به این ترتیب میتوانید برنامه تولید را در افقهای بلندمدت و میانمدت تهیه کنید و نیازمندیهای تولید را در دوره تخصیصداده شده، مشخص کنید.
سپس میتوانید منابع تولید را با توجه به ظرفیتهایی که از پیش در ساختار محصول، مسیرهای تولید، شیفتها و تقویم کاری تعریف شده، به همراه توقفهای پیشبینی شده و پیشبینی نشده تولید در نظر بگیرید تا برنامهریزی و زمانبندی تولید را ایجاد کنید. به این ترتیب راهکار برنامهریزی و مدیریت تولید نوماتک به شما کمک میکند برنامه تولید بلندمدت (یک یا چند ساله) واحد تولیدی خود را محاسبه کنید و به راحتی آن را در بازههای زمانی کوچکتر، در برنامههای میانمدت و کوتاهمدت با جزئیات بیشتر مشاهده کنید.
درخواست دمو
برنامهریزی بلندمدت
دستور تولید
دستور تولید
دستور تولید، یک برنامه اجرایی و دستوری عملیاتی است که براساس برنامه تولید در دوره زمانی کوتاهتری تهیه میشود. راهکار برنامهریزی و مدیریت تولید با در نظر گرفتن نیازمندیهای مواد و نیازمندیهای ظرفیت واحد تولیدی، محاسبات برنامهریزی تولید را انجام میدهد و دستور تولید بر اساس برنامه تولید ایجاد میشود. دستور تولید به شما میگوید یک واحد تولیدی چه مقدار ماده اولیه را در چه تاریخی برای تحقق برنامه تولید باید در اختیار داشته باشید و از ظرفیت ماشینآلات و تجهیزات به چه صورت استفاده کنید تا به بتوانید برنامه تولید را محقق کنید.
وقتی برنامه تولید را به دستور تولید تبدیل میکنید، به واسطه دید جزئیتری که در دستور تولید وجود دارد، توقفهای تولید، سفارشهای لغوشده و هر گونه تغییرات در زمانبندی سبب تعدیل در سطح تولید، بهکارگیری ماشینآلات، مواد اولیه و ... میشود. به این ترتیب با توجه به نیازمندیهای مواد، درخواست مواد اولیه (با توجه به سیاستهای تولید عموماٌ) به انبار داده میشود که در صورت عدم موجودی، منجر به صدور درخواست خرید (با مقدار و زمانبندی تحویل معین) خواهد شد (در تولیدهای گسسته سفارشگذاری بر اساس اندازه دسته محصول تولیدی (lot size) صورت میگیرد).
راهکار برنامهریزی و مدیریت تولید نوماتک به شما کمک میکند دستور تولید را به صورت عملیاتی بر اساس محاسبات برنامهریزی تولید ایجاد کنید، عملیات و اولویت عملیات برای تولید محصول نهایی را مشاهده کنید، نیازمندیهای ظرفیتی و مواد اولیه را در اختیار داشته باشید و توقفهای تولید را در نظر بگیرید.
ویژگیهای نرمافزار ثبت عملیات تولید
یکی از ارکان اولیه در مدیریت تولید، ثبت عملیات تولید است تا به این ترتیب بتوان روند تولید را کنترل کرد. راهکار نرمافزاری برنامهریزی و مدیریت تولید نوماتک به شما کمک میکند بتوانید با تعریف برگههای تولید بر اساس پارامترهای مورد نیاز خود، عملیات تولید، مصرف و ... را با جزئیات ثبت کنید.
تعریف برگههای تولید
برای ثبت عملیات تولید لازم است از برگههای ثبت عملیات متناسب با نیازمندیهای خود استفاده کنید. به بیان دیگر نوع فرایند است که اطلاعات برگههای ثبت عملیات تولید را مشخص میکند. با استفاده از نرمافزار نوماتک میتوانید مواردی مانند مقدار تولیدشده، مقداری که در دستور تولید بوده و انطباق این دو را در برگههای ثبت تولید یادداشت کنید، این مقادیر را با مقادیر روزهای قبل مقایسه کرده تا در نهایت بهتر بتوانید انطباق تولید و هدف تولید را مقایسه کنید. علاوه بر برگههای ثبت عملیات تولید، برگههای ثبت تعدیلات تولید را نیز میتوان ایجاد کرده و موارد مربوط به تعدیل در تولید را گزارش کرد که به این ترتیب این تعدیلات به صورت خودکار مقادیر تولید در برنامه تولید را نیز تعدیل میکند.
درخواست دمو
تعریف برگههای تولید
ثبت عملیات تولید
ثبت عملیات تولید
ثبت اطلاعات لازم از عملیات تولید در برگههای ثبت عملیات (که پیشتر بر اساس پارامترهای مورد نظر خود تعریف کردید) به شما کمک میکند میزان تولید، مصرف، عملیات، توقفهای تولید و ... را در هر دوره زمانی در اختیار داشته باشید. به این ترتیب علاوه بر اینکه فرایند تولید خود را تحت کنترل خواهید داشت، میتوانید با بررسی روند اطلاعات، به راحتی ریشه برخی مسائل تولید مانند عقب ماندن از برنامه تولید، افزایش ضایعات و سایر کاستیها را شناسایی کنید.
درخواست دمو
مدیریت توقفهای تولید
توقفهای تولید در هر واحد تولیدی بسته به محصول تولیدی، ماشینآلات و سایر منابع تولیدی ممکن است دلایل متفاوتی داشته باشد. برخی از توقفها پیشبینی شدهاند؛ دلایل مشخصی مانند لزوم سرویس یا تعمیرات دورهای ماشینآلات، تعطیلات از پیش تعریف شده و ... وجود دارند که سبب توقف تولید میشوند. دسته دیگر توقفها پیشبینی نشدهاند و دلایل مشخصی ندارند؛ مانند حوادث یکباره، خرابی ماشینآلات، تأمین نشدن به موقع مواد اولیه و ... . در هر صورت این توقفها باید در برنامه تولید در نظر گرفته شوند. شما میتوانید فهرستی از دلایل توقفهای خط تولید خود را ثبت کنید تا بعدتر بتوانید از آن در ثبت توقفها استفاده کنید. همچنین میتوانید برنامه تولید را بر اساس توقفهای پیشبینی شده ایجاد کنید و سپس به صورت روزانه بر اساس توقفهای پیشبینی نشده در صورت لزوم آن را تعدیل کنید. این تعدیلات سپس به صورت خودکار در دستور تولید نیز اعمال خواهد شد.
درخواست دمو
مدیریت توقفهای تولید
ثبت مستقیم عملیات تولید
ثبت مستقیم عملیات تولید
ثبت عملیات تولید را میتوانید همچنین به صورت خودکار و مستقیم از طریق ماشینآلات انجام دهید. به این ترتیب خروجی عملیات تولید در قالب یک فایل اکسل از ماشینآلات دریافت و در سیستم بارگذاری میشود.
درخواست دمو
جستجوی پیشرفته برگههای تولید
با استفاده از امکان جستجوی پیشرفته میتوانید به آسانی مقدار یک پارامتر مشخص مورد نظر خود را در تمام برگههای تولید جستجو کنید. به این ترتیب امکان مقایسه پارامتر مورد نظر مثلاً با مقادیر مورد نظر را نیز خواهید داشت.
درخواست دمو
جستجوی پیشرفته برگههای تولید
مدیریت سطوح دسترسی به برگههای تولید
مدیریت سطوح دسترسی به برگههای تولید
افرادی با مسئولیت مشخص میتوانند اطلاعات لازم را در برگههای ثبت عملیات تولید وارد یا مشاهده کنند. همچنین در مورد ثبت تعدیلات نیز چنین شرایطی وجود دارد.
نظر شما در مورد این مقاله چیست؟
نظرات کاربران
مقاله مرتبط
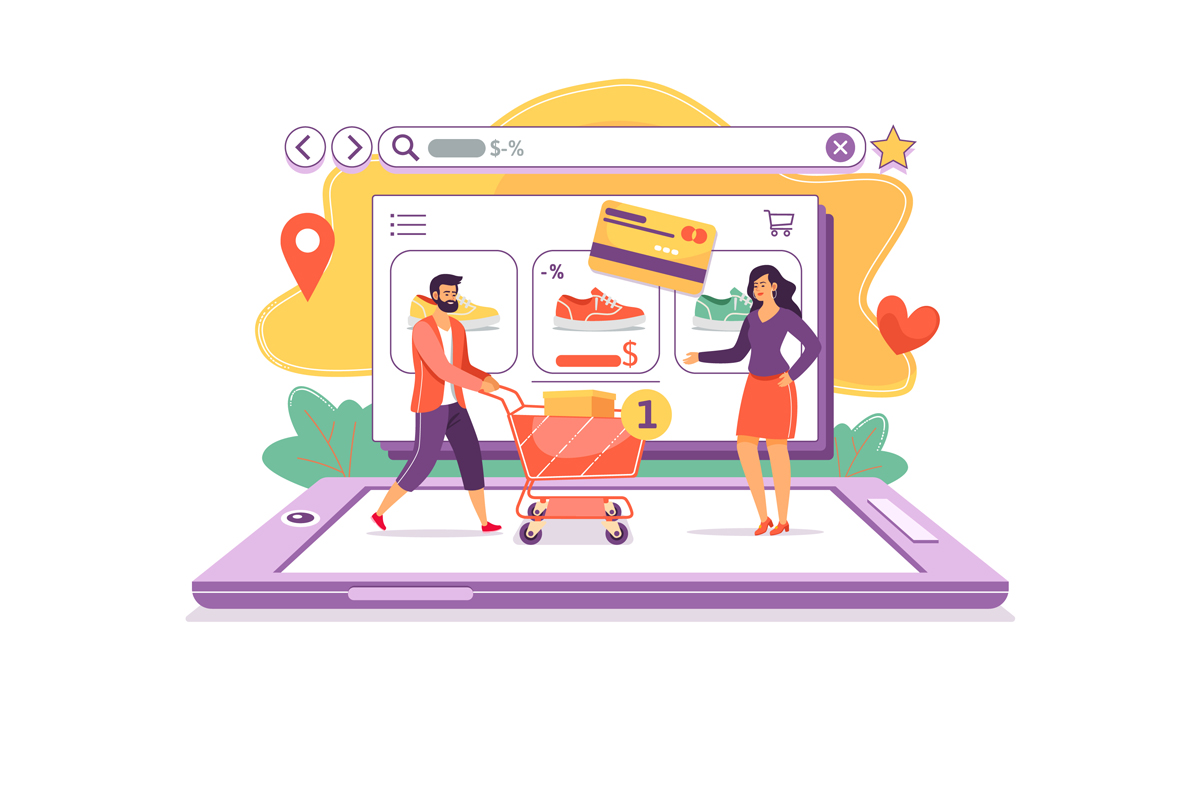
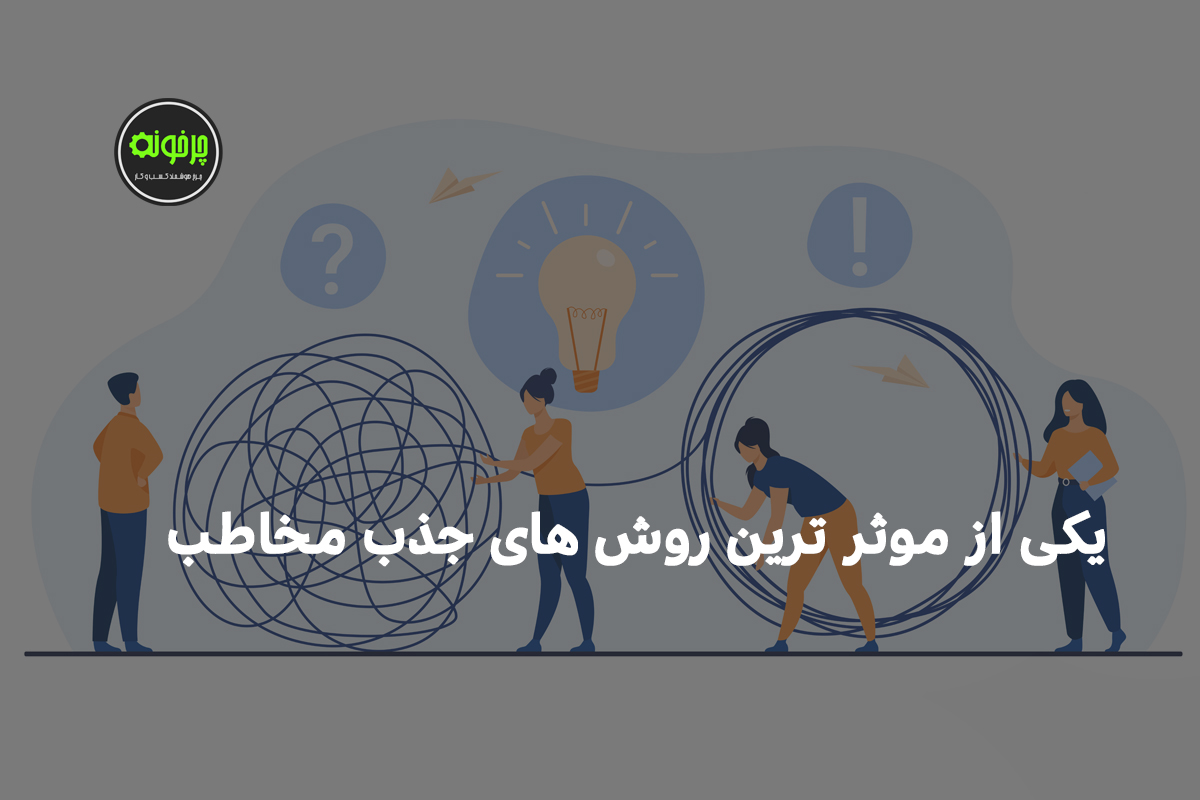

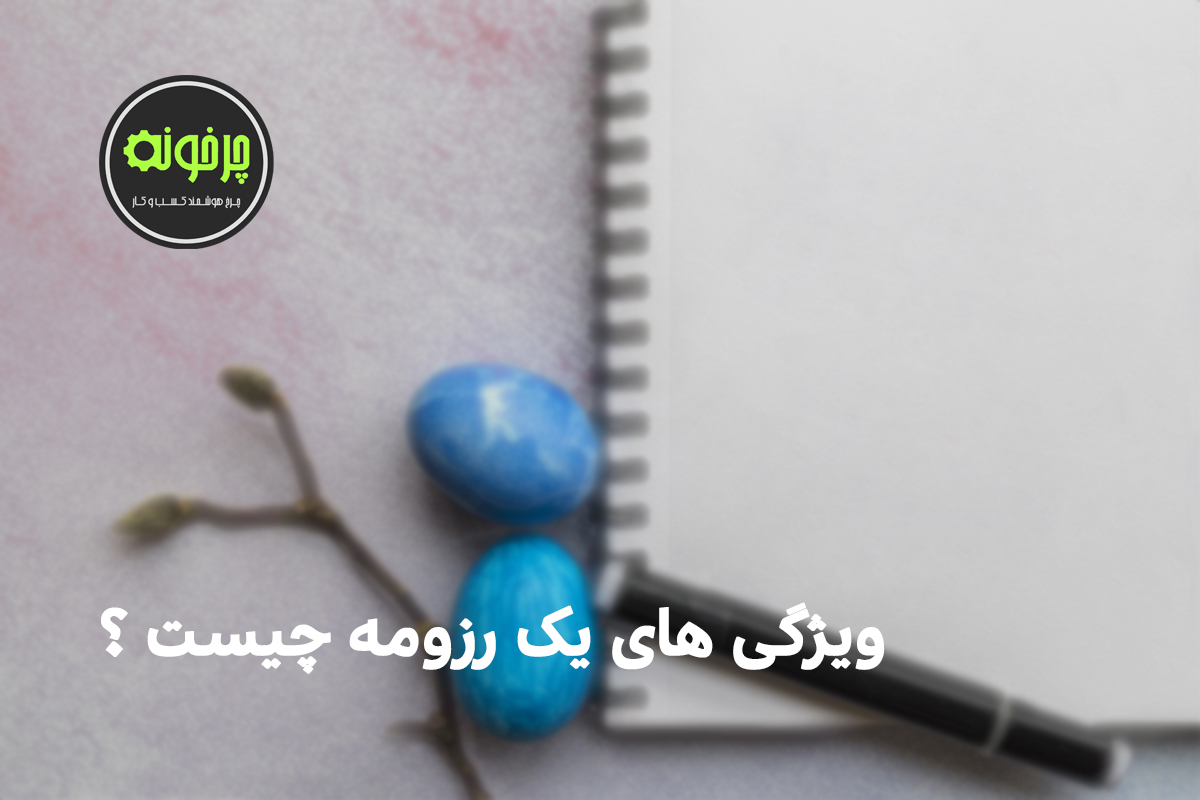